How external blinds are produced step by step
At the point when a customer orders external blinds from us, we get a perfectly adjusted production process going, which results in a finished and conscientiously packed product. Read how we manufacture external blinds at NEVA.
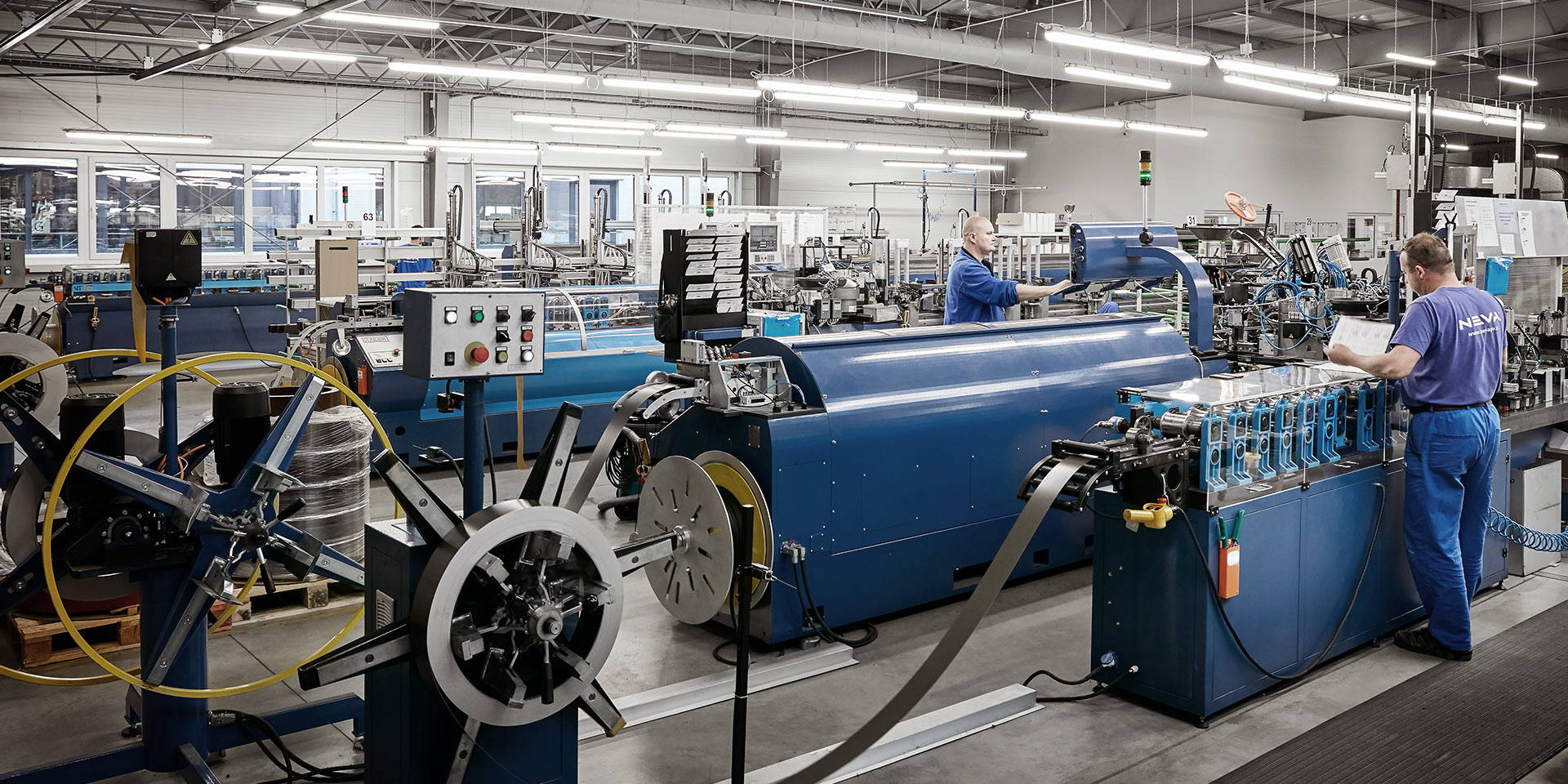
By rolling the material for slats we give shape to our blinds
The production of external blinds always starts on the rolling machine. We’ve got over ten rolling mills on six rolling machines in operation at NEVA. Two of them are dedicated to the most popular Z90 shape, and we can adapt others flexibly based on our production needs. We roll 6 types of external blinds at the moment:
The dimensions of the blinds along with the unique order number go into the rolling machines directly from the ordering system. The colour of the slats is monitored by the machine operator. As a result, the situation where we make a dimensional error in production or manufacture an incorrect type of blind is virtually impossible.
When you come and stand in front of the rolling machine, you can see at one end how the machine pulls in the material for slats, then the machine automatically feeds it over the rolling discs, and the finished slats come out on the other side – with the necessary holes for the lift tape, with the hooks for putting the ladder on as well as with the guide pins. Finally, the machine automatically puts the positioning ladder on the slats, creating a so-called packet of blinds.
The slats are checked by lasers all the time so that they are rolled with millimetre accuracy. The operator oversees all this just in case. Moreover, the operator also checks the strength of the slats by random destructive tests, adjusts the machine for atypical orders and marks packets of blinds manufactured with labels for correct completion of the order.
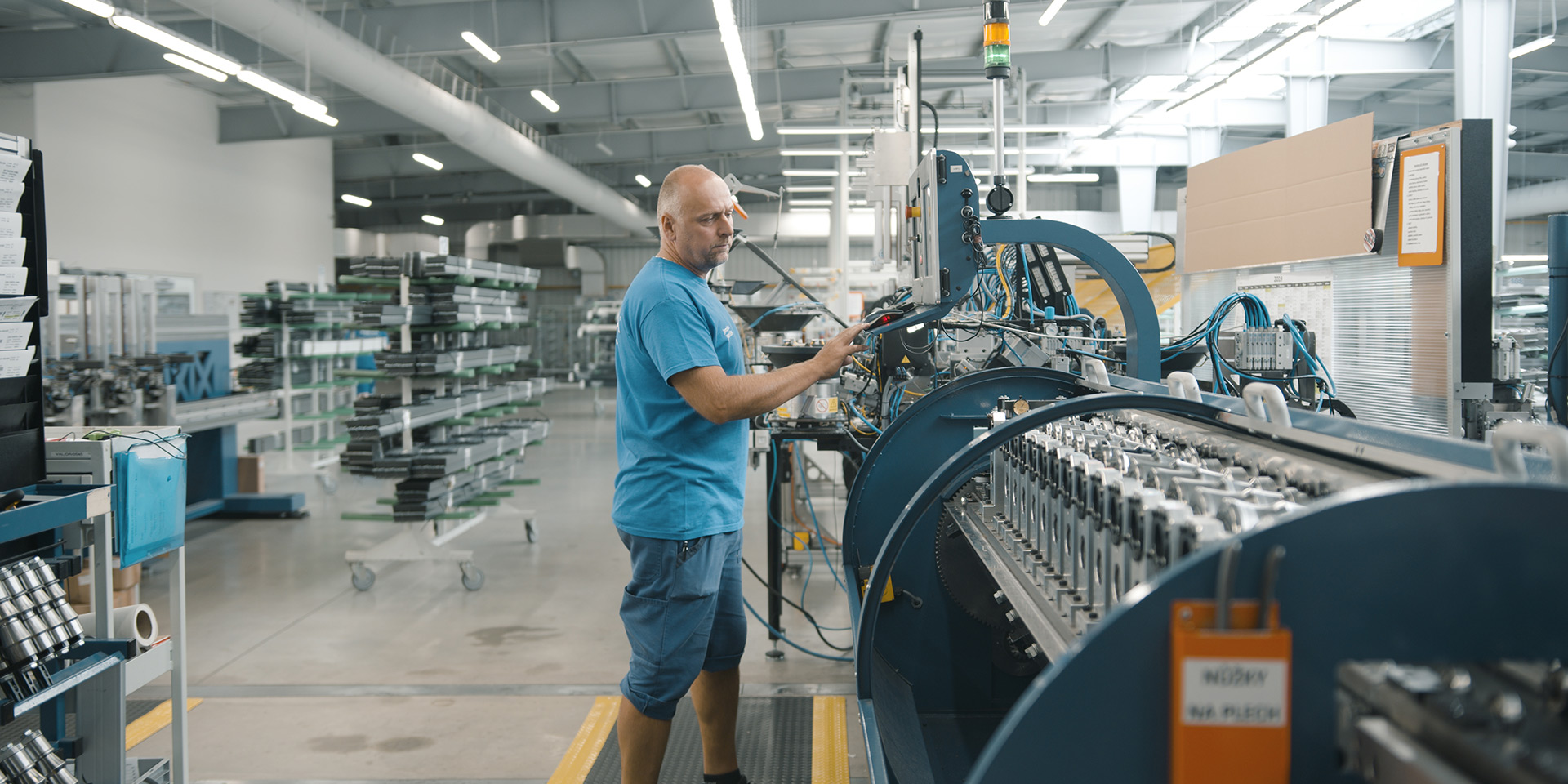
We pay great attention to the quality of the paint. We’ve been purchasing, on a long-term basis, the materials for slats from Swiss manufacturer Metalcolor, which employs the method of multiple wet painting of the sheet metal. Top quality is of paramount importance to us and we’re absolutely satisfied with this product.
Slats that have been rolled correctly may only come out of a well-adjusted rolling machine. That’s why we also focus our attention on the servicing of our rolling machines. At the beginning of the shift and always after a new batch of material for slats (a new coil or colour of sheet metal) has been loaded in, we first produce a test slat. The test slat serves solely for the rollers to verify that everything is OK. If something is amiss, we stop the rolling machine immediately, check it and carry out maintenance. Naturally, we roll a test slat after every service operation as well.
Rollers further continue to monitor the machine so that they can immediately detect any problems that may arise. As soon as they register an error message on the control panel, spot metal filings in the machine or hear an unusual sound, they stop the rolling machine and deal with the problem immediately.
To prevent snags in production we carry out service inspections of the machines at regular intervals.
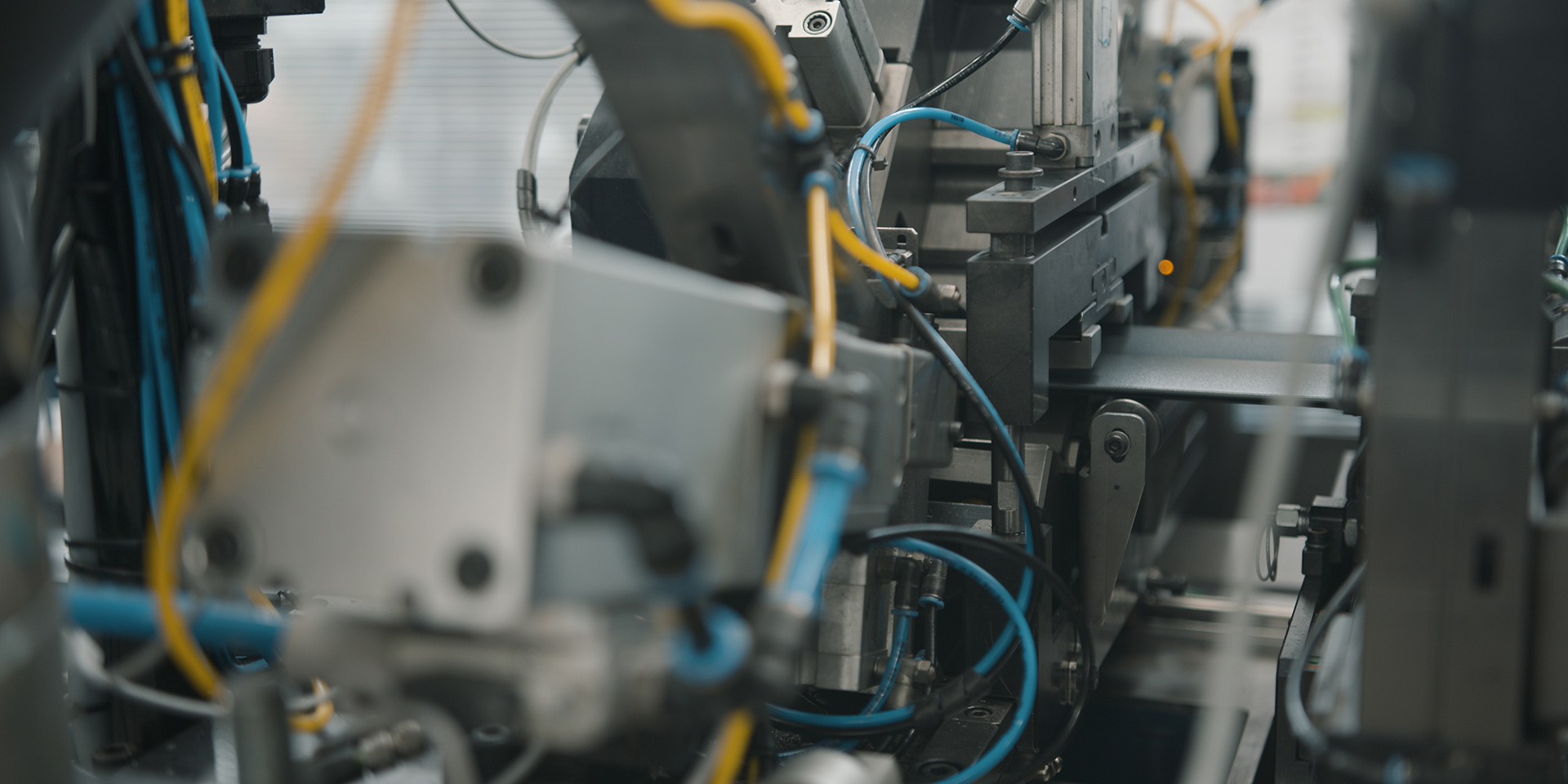
Thanks to our own paint shop we can vouch for the colour of our accessories
Besides slats, the blinds also need upper and lower profiles and guide elements – side cords or profiles. As standard, we supply upper profiles made of galvanised steel and we roll them ourselves.
We paint the lower and guide profiles from an external supplier in our own paint shop so that they conform precisely to the customer’s requirements. Previously, we would have the accessories painted elsewhere. As we wanted to have the delivery time and quality fully under our control, we opened our own powder paint shop in 2014. If you wish to learn more about painting, please read this article or look at the interview with the head of our paint shop.
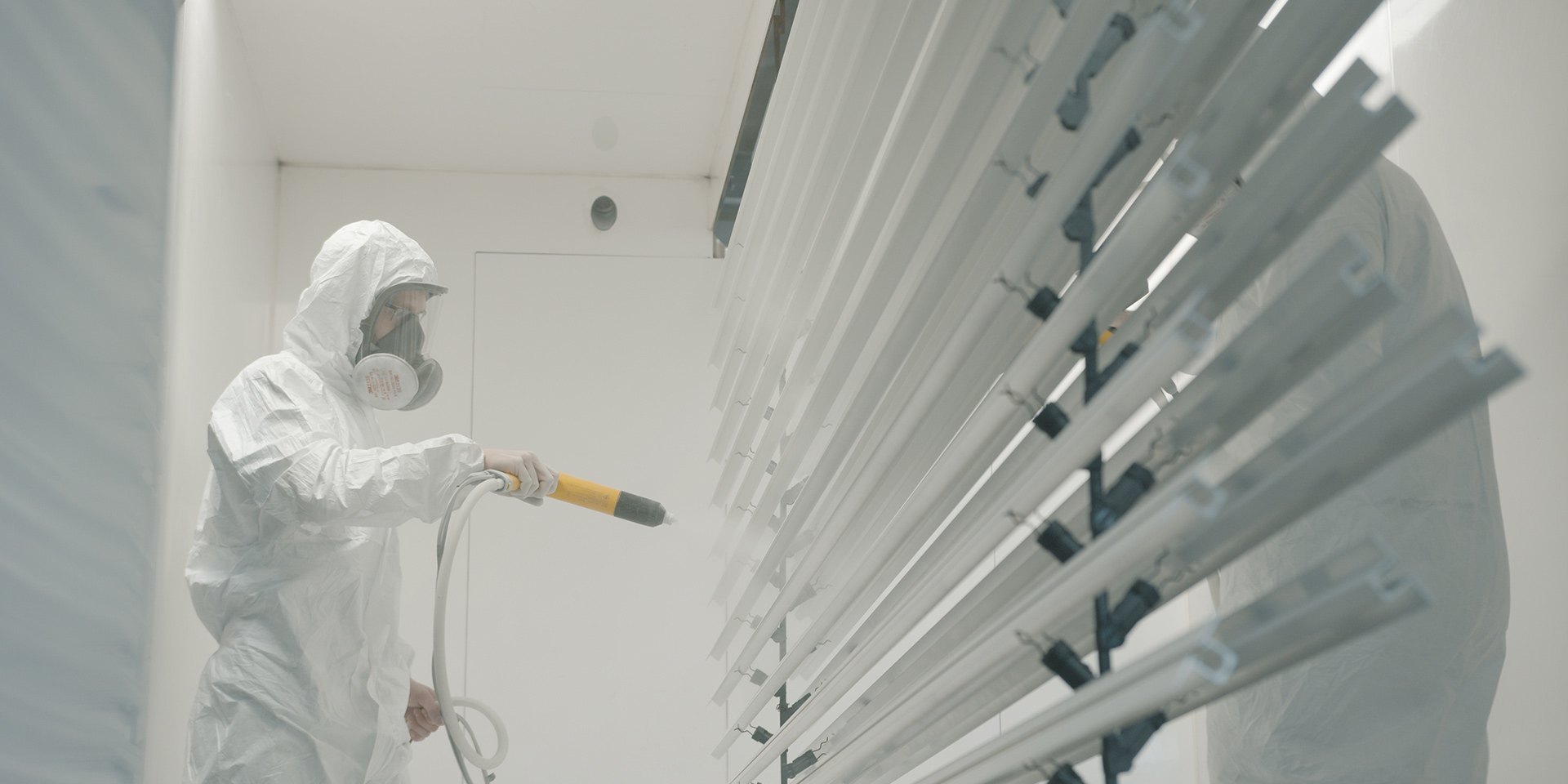
We mount most often an electric drive of blinds
The upper profiles head to another workshop, where we manually add the control mechanism to them. External blinds by NEVA may come with crank control or with a motor drive. We supply our products with Somfy motors but our customers may opt for the Elero or Geiger brands as well.
Our technicians deal with up to 1,300 motors every week.
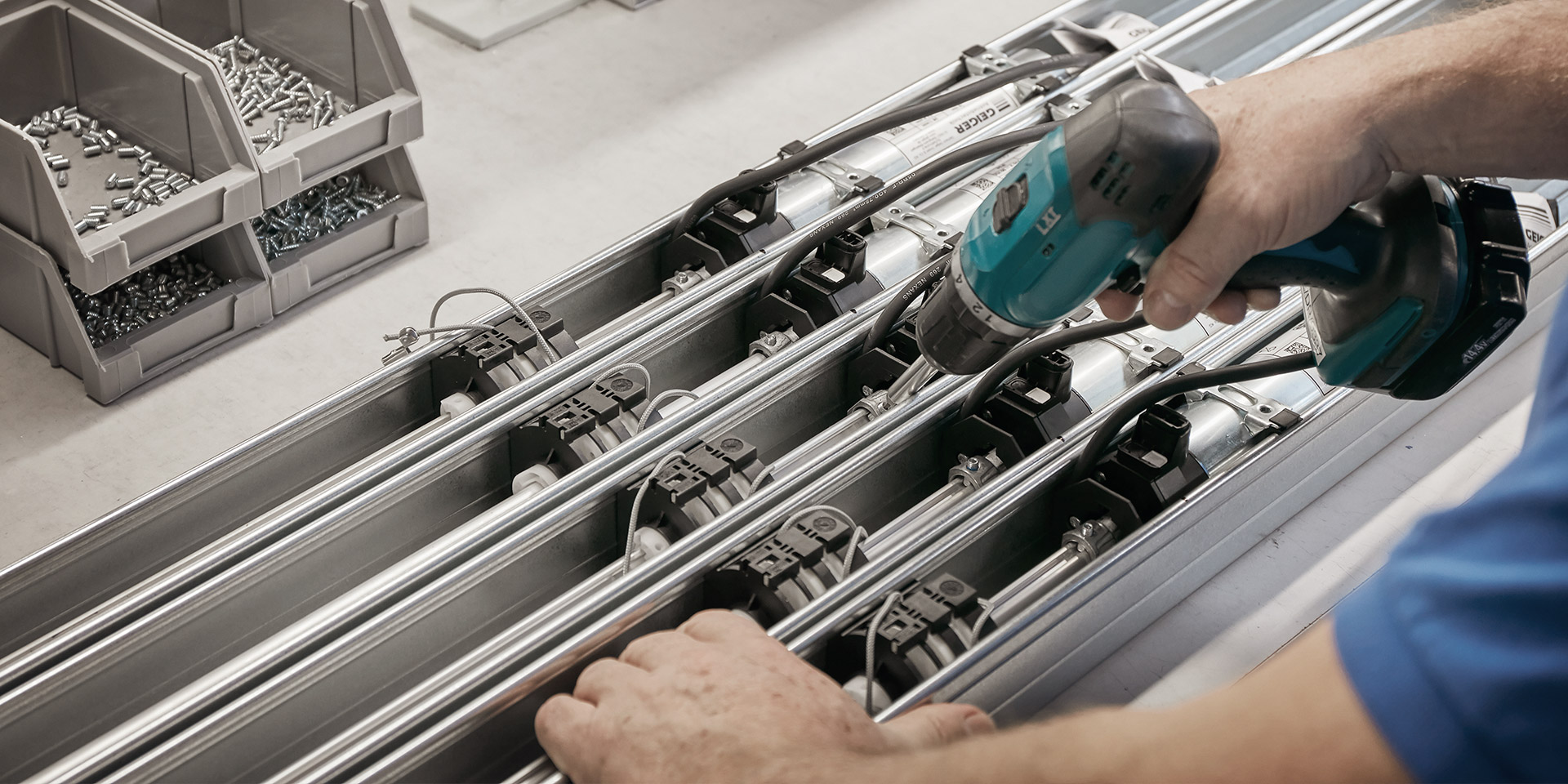
Assembling, setting the end positions and inspection all in one place
If the order is non-standard, all the components of the blinds are prepared in advance so that the assembly workers can have everything at their disposal and don’t have to search for or collect anything from the warehouse. Thanks to that, there are no delays in searching for the necessary material.
During assembly we connect all the parts of the blind together. We start by threading the lift tapes through the slats. Then we adjust the upper and lower end positions of the motors in such a way that the blinds have enough space for the slats to be tilted. This considerably facilitates installation directly on the construction site and shortens the mounting time. At the inspection workplace we verify whether the lower profile is perfectly flat and the dimensions as well as other parameters of the blind conform precisely to the order. In the end, we inspect everything visually once more.
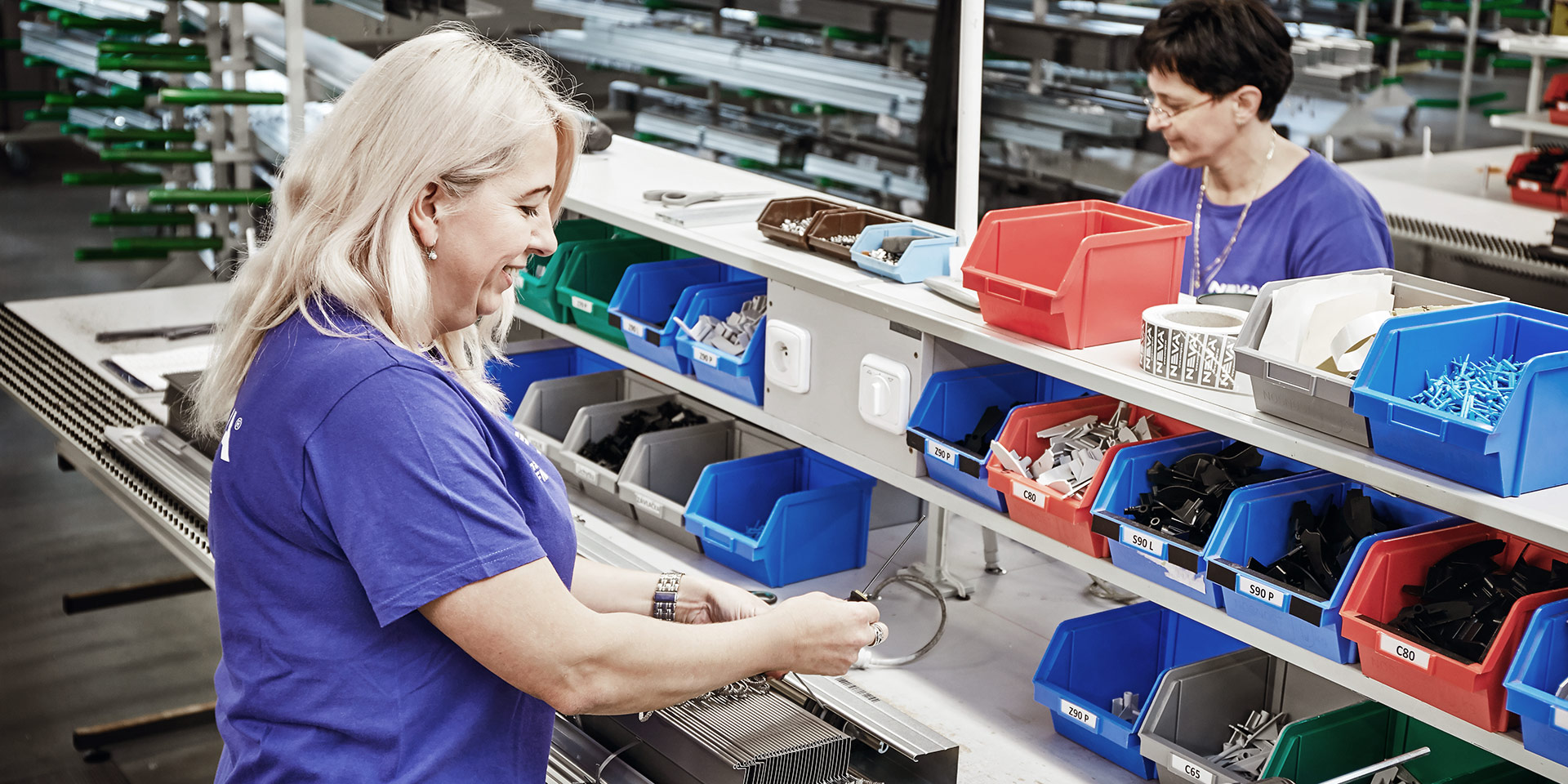
We know exactly which slat has been rolled by whom
Since we consistently keep to the promised time limit for production within ten working days with respect to standard orders, every step in the production process is critical. Nothing must be delayed. That’s why we keep large stocks of the material for slats, accessories and powder paints.
To ensure that production runs as efficiently as possible, we have a planner who coordinates the production so that we produce identical shapes of blinds in the same colour successively. What’s more, we make individual parts of blinds in parallel, thanks to which all the components come together during assembly at the same time.
If we’re going to produce a non-standard item, we check the availability of the components both in our warehouse and at our suppliers’ immediately after the enquiry has been sent to us so that you can arrange particular dates and the final price with the client.
We monitor each blind from the moment it is entered into the job system by means of its unique number and bar code. The operators “beep” to indicate every step during production, i.e., confirm electronically that they’ve done the necessary work. Thanks to that, we know exactly who produced, mounted, painted and tested which component and when.
We place emphasis on safety when packing and despatching our products
We supply NEVA blinds all around the world – besides Czechia, for example, to Germany, Scandinavia, Israel, Japan and Australia. We care for the quality of the packaging, too. As early as when completing the order, we insert protective polystyrene cubes in between the upper profile and the slats so that the parts don’t get scratched; we protect the edges of the slats and guide pins with polystyrene side walls, and put wrap around the ladder to prevent it from breaking during transport.
If the order is to be transported by our delivery service, we pack the blinds only in bubble and shrink wrap to spare the environment, to limit the production of packaging and make it easier for installation workers on the site to unpack the blinds. Our drivers know how to handle our products.
If the order is to be transported by external carriers, we pack the blinds additionally into carton boxes. Thanks to the Panotec formatting machine, we can make a box that exactly fits the size of each blind to prevent it from moving or getting damaged inside. Thanks to these boxes, we’ve seen a marked decrease in complaints owing to transport.
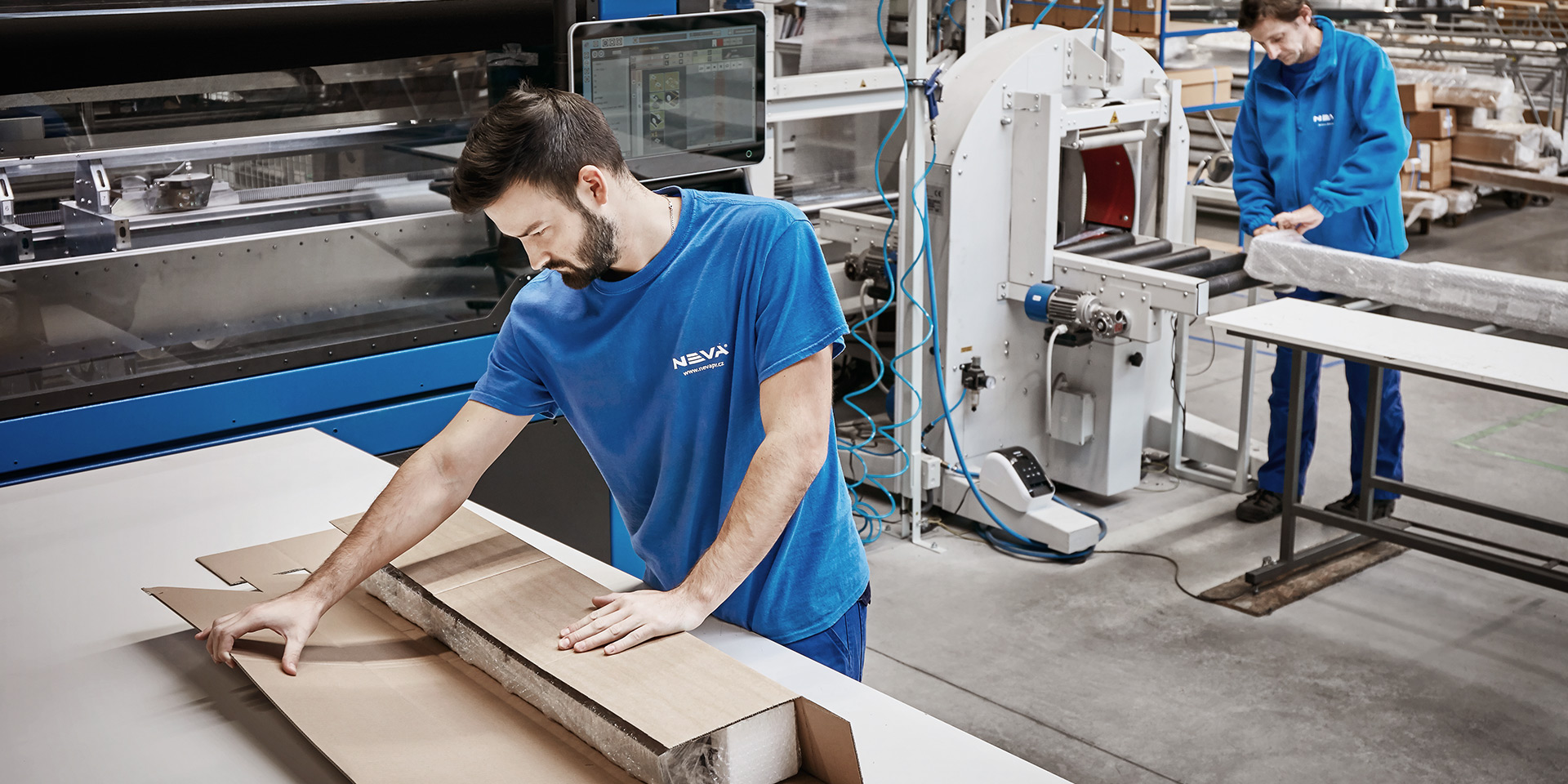
For ship and air transport we put the blinds into cases we manufacture in our own joiner’s shop. Our goal is again maximum protection against damage.
If you wish to see the entire coordination of our production live, arrange a date with us and we’ll be pleased to show the entire production process at NEVA.