We paint all blind components by hand. Do you know why?
We place great emphasis on correctly painting the blind components. What are the benefits of hand powder coating and what role does cleanliness play? Read about the processes in our paint booth and the expected final treatment of the components.
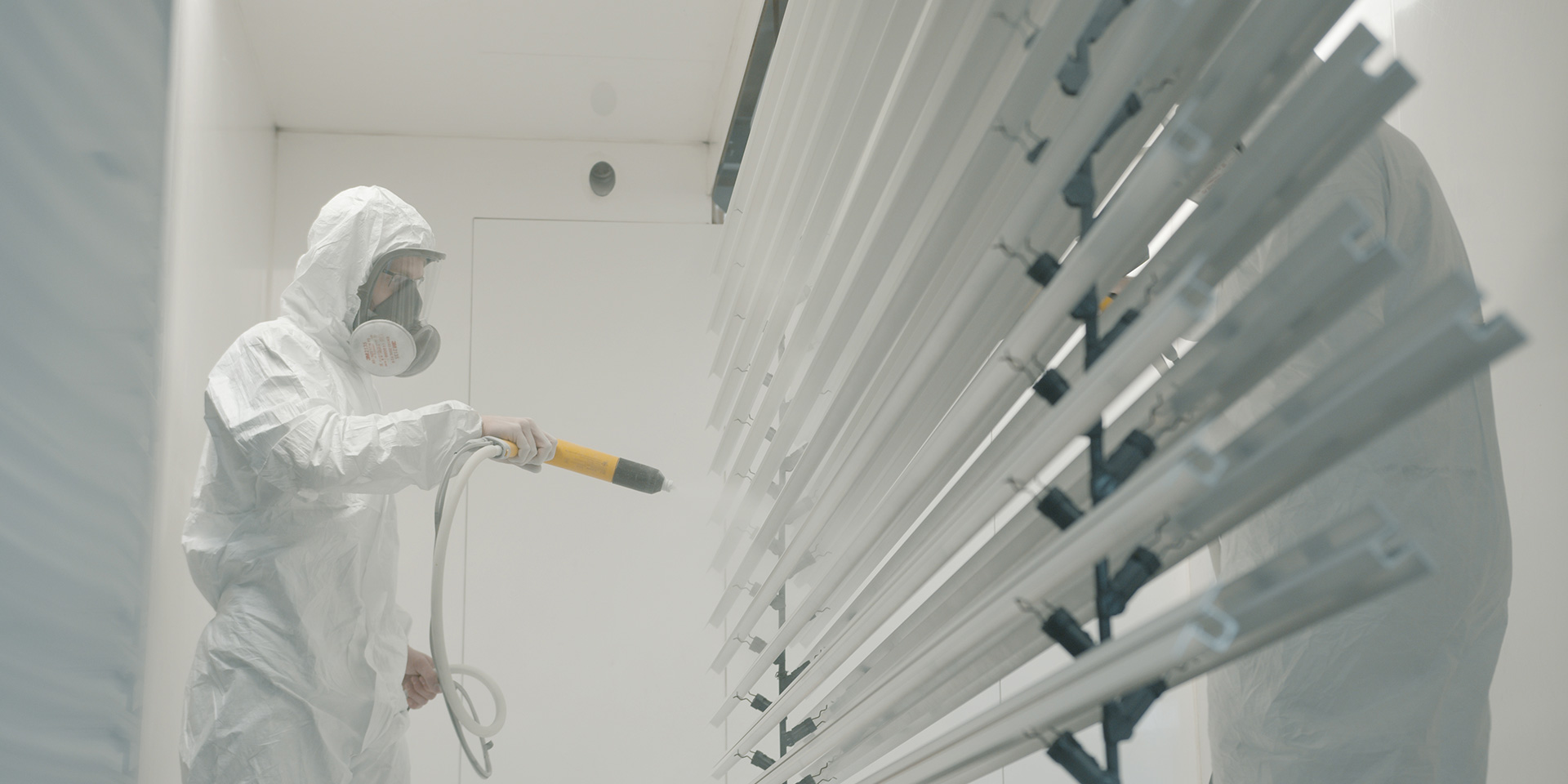
We paint on our own painting line
If you visit NEVA, you will see our operations including the semi-automatic powder coating line. Since 2014, we have been applying powder paint to the blind components on our own. Therefore, we have full control over the deadlines and the resulting quality of orders.
This turned out to be the right decision because our own powder coating shop significantly speeds up our work. The durability and resistance of the surface have been proved by thousands of customers all around the world.
All our
- holders,
- guiding rails,
- bottom profiles
- and cover plates, pass through our powder coating shop.
We do not paint the slats because we import them already painted from a world leading manufacturer in Switzerland. The manufacturer paints the slats using a wet painting method, which is suitable for large areas and is also used, e.g., in the automotive industry. By contrast, we paint the blind accessories using a powder (dry) paint.
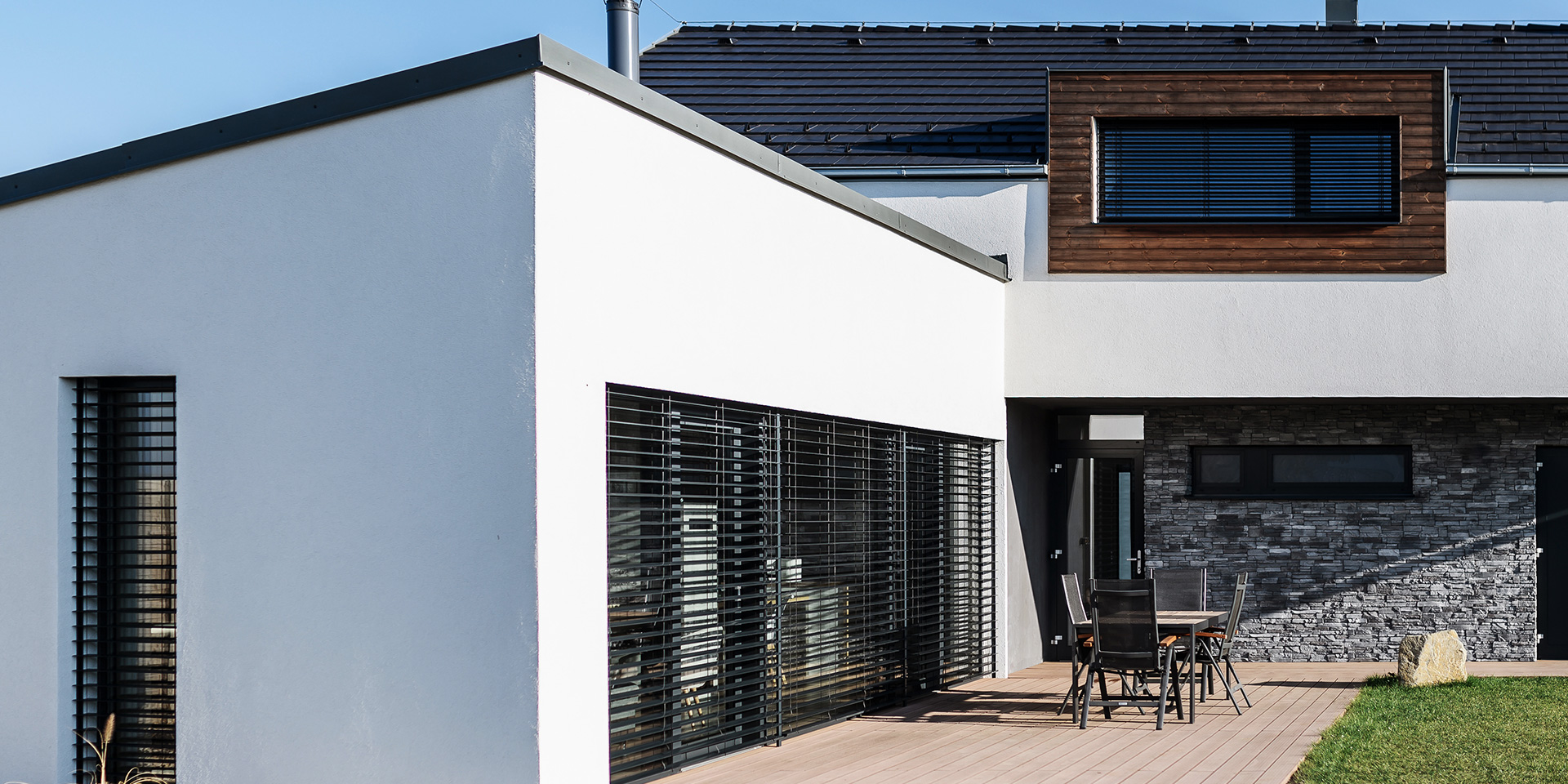
Technology step by step
Powder coating is a long-proven technology in the Czech Republic. You can also refer to it as comaxite application or dry painting. The whole process has several steps and clear technological procedures.
Step 1: Component preparation
We check all guiding rails and bottom profiles, remove surface dirt on a brushing machine and roughen the surface. We need to ensure that the powder paint sticks to the surface. We remove the film that protected the surface during shearing and bending.
Step 2: Hanging the parts
We hang all parts on a paint hanger, which is part of the semi-automatic enclosed rectangular conveyor line. We hang components up to 1,500 mm high and 6,000 mm long on the hanger.
Step 3: Chemical pre-treatment
The components travel to an automatic spraying line, which consists of two chambers. They spend 30 minutes in both chambers. The first chamber degreases the surface of the components by an acid agent, deoxidizes them and rinses them with water. The second chamber rinses the components with demineralized water so that a titanium conversion nano-layer is formed and rinses them again with demineralized water.
Step 4: Drying after chemical pre-treatment
We dry the hangers with the components in a direct-firing gas oven at the temperatures up to 150 °C. Hot air circulates around the components for 30 minutes, perfectly drying the surface including all folds.
Step 5: Powder paint application
The dry components travel to the painting booth where we apply the powder paint by hand using an electrostatic method. The painting process is based on charging the powder particles with an electric charge and earthing the painted component. This creates a force that keeps the powder on the surface of the component in a sufficiently thick layer of paint.
Step 6: Powder paint hardening
After powder paint application, we transport hangers with the components to a direct-firing gas oven where the paint hardens within 20 minutes at the temperatures up to 200 °C.
Step 7: Cooling and unhanging
When the material leaves the paint drying oven, we allow it to cool and then unhang it onto the handling carriages. They will stay there for another 24 hours to allow the paint to harden completely.
Step 8: Inspection and packaging
When the painted components cool, we visually check them one by one, measure the thickness of the paint layer and the gloss level. Then we perform destructive tests on test samples that passed through the same process with the painted components. When the components comply with the required quality parameters, we pack everything according to the customer’s requirements.
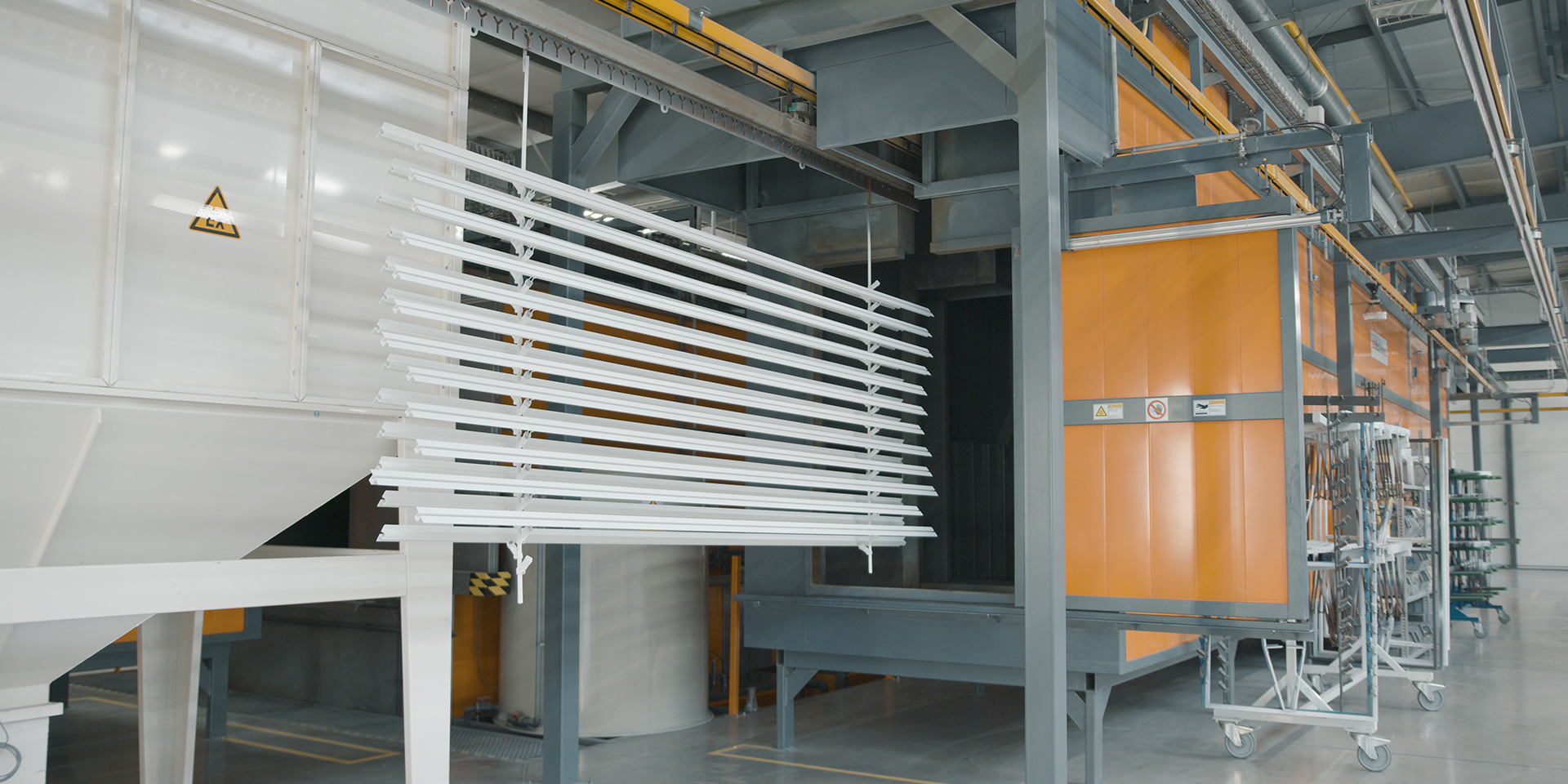
Why is hand painting beneficial
We paint the blind accessories in hundreds of shades according to the RAL and the NCS samplers. Each type of component is variously shaped, which entails great demands for even paint application. Therefore, we paint all surfaces including edges and corners by hand so that the powder paint covers and protects the whole product.
We apply the paint by hand using a spray gun. The spray gun nozzle is equipped with an electrode where high voltage of 30-90 kV is concentrated to ionize airflow passing through the gun. When passing through the ionized air, the powder particles are covered by free ions, thus charging them negatively. If the painted components are correctly earthed, this technology guarantees a perfect result even in case of very complex parts.
The sprayers have high merit for the final looks of the components, working in demanding conditions of the paint booth when painting complicated shapes of the products. Other colleagues do not allow an imperfect component to leave the production during inspection of the complete accessory.
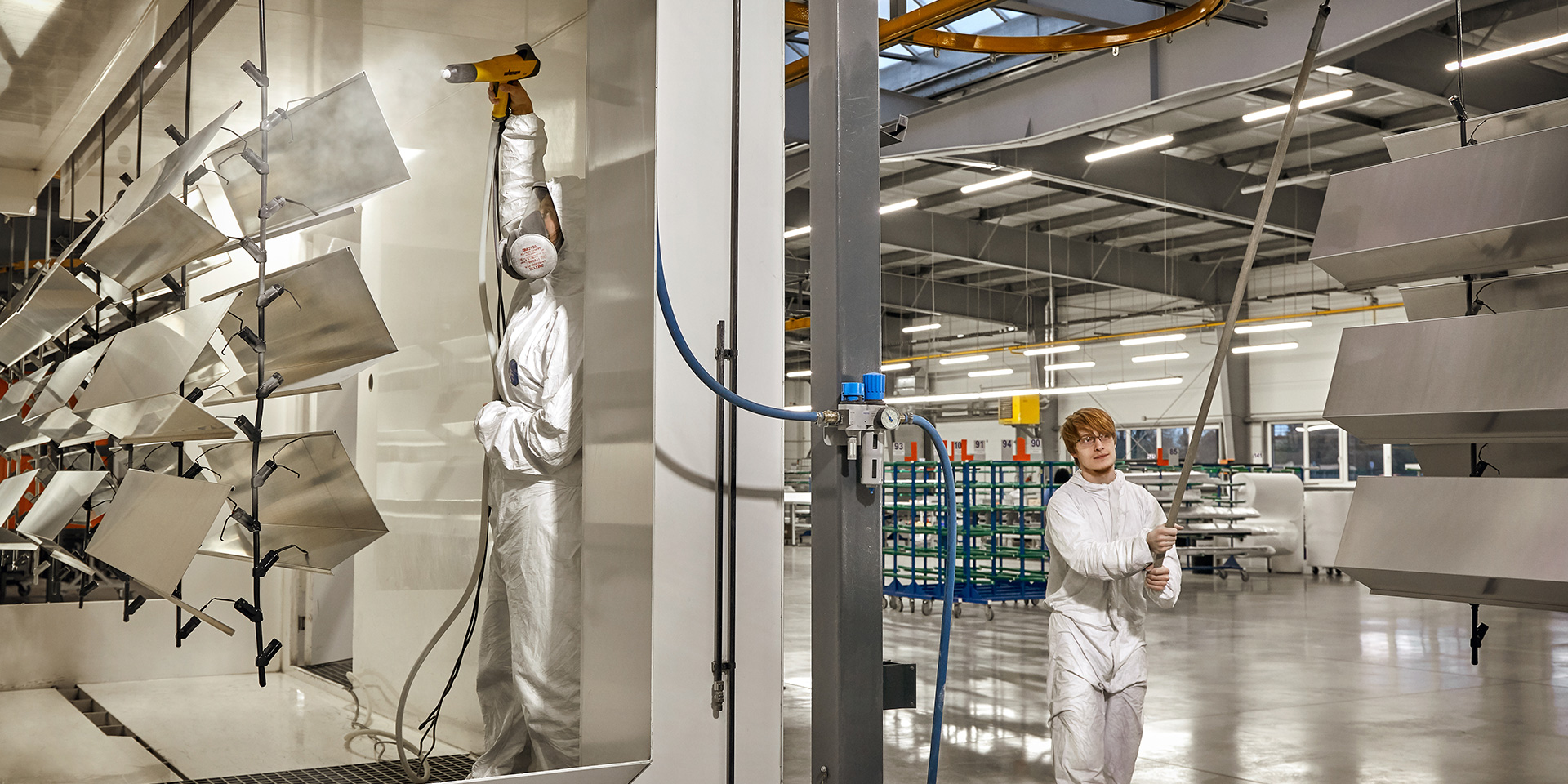
Cleanness is half of the success
Painting of accessories is subject to over-spraying, which sticks to inner walls of the booth and around it. The residual powder paint is extracted by a fan, which sends the unused powder to the final filters via a recycling cyclone with the force of 18 thousand cubic meters per hour. This separated powder paint is not reused but disposed of in an environmentally friendly manner. Clean air returns back to the paint shop.
After each application of one shade, we always clean the booth with compressed air to prevent mixing the colours when a new shade is used. When cleaning the paint booth, the residual paint is extracted by the final filter fan under strong negative pressure.
This prevents:
- mixing of individual shades,
- negative impact on the resulting painting,
- polluting the space around the paint booth,
- aggravating the sprayers’ working conditions and their health.
Do you want to see the whole process with your own eyes? Reserve a date and come to see our paint shop.