How many times per day do our painters change their work attire and why? The powder coating plant manager reveals how things work behind the scenes
We used to coat the components of our blinds at other plants, but were not satisfied with the results. For this reason we built our own in-house powder coating plant in 2014. Read the interview from behind the scenes of the blind powder coating process and learn about the communication signals of the painters, why the quality of the powder-coated blinds is checked mainly by women and how many times a day the painters change their work attire.
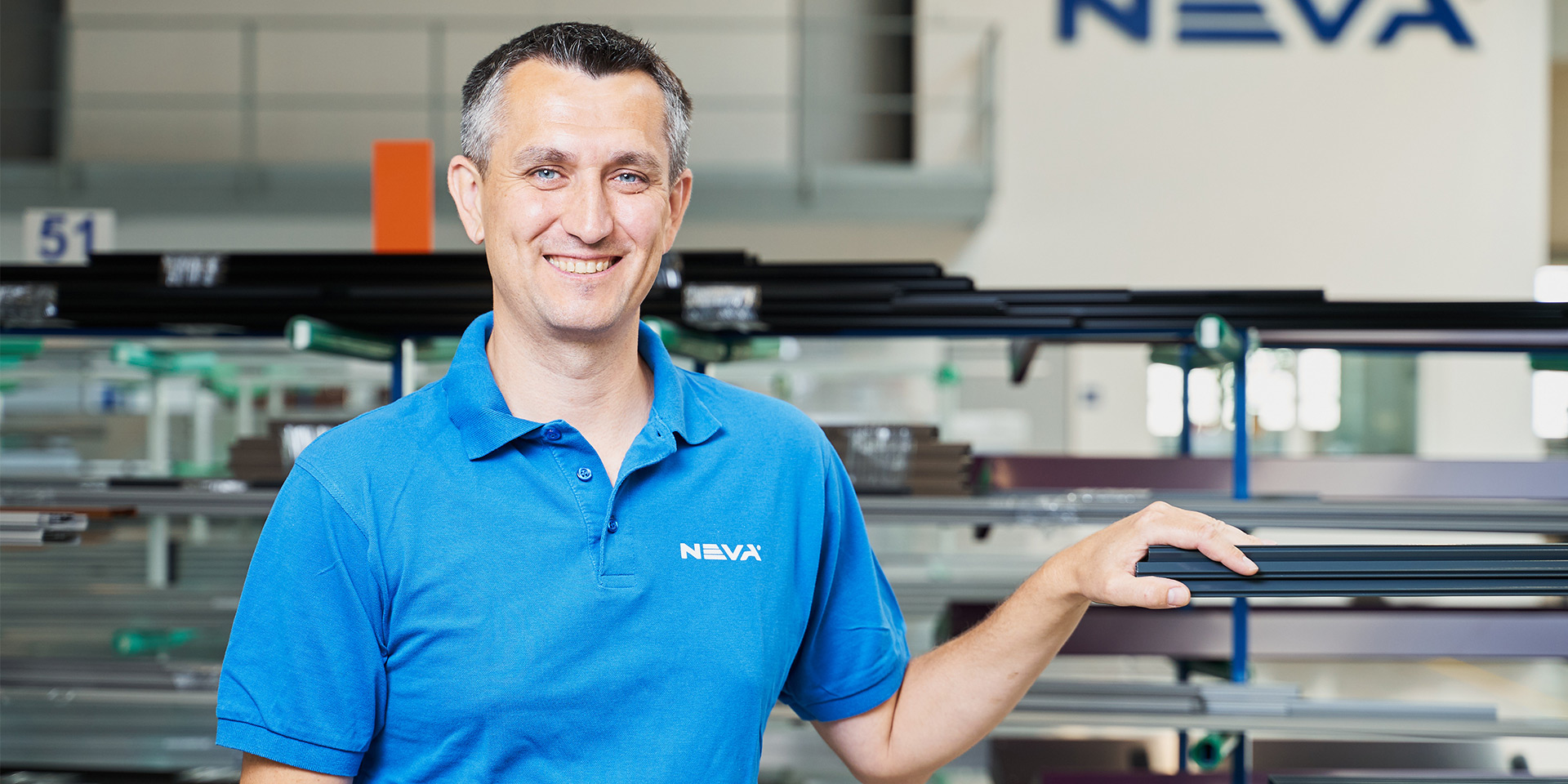
What was the most difficult thing that you encountered during the start-up of the powder coating plant in 2014?
Several obstacles emerged at the beginning. The worst problem were the impurities that fell on the painted material when the line operations started and thus debased the material. The design of the powder coating line was to blame for this. We needed to run in the line as quickly as possible for all the components and mechanical parts to fit together and ensure that they did not release metal shavings, impurities or oil.
So you could only wait?
Not at all. We made an effort to eliminate the impurities in all possible ways. We kept cleaning and grinding the components over and over again. Fortunately, it worked.
What are the specifics of the blind component coating process?
The specific aspect is that we have various types of products and each of them has a different shape. We paint the large surfaces of cover sheet-metal, narrow guiding rails and bottom profiles or holders for profiles with a lot of bends which the painter has problems painting. And it is because of the combination of these three types of products that it was difficult to debug the process and get everything to work.
We powder coat the blind components within 6 hours
Why did you opt specifically for powder coating?
Thanks to it, we can easily get into the bends of complicated components. Powder coating is moreover a quick and more ecological painting method. Unlike the wet method, no solvents are used in the process so the environmental pollution is lower. And it is mainly quick and we can paint the product within 6 hours. Wet painting takes much longer.
Does the NEVA procedure differ from that in other companies?
At NEVA, everything starts with preparation of the material for painting. It is a stage that we rely on. When we started painting, we ascertained that many scratches and faults in the material are visible only after painting. For this reason, we brush the profile surfaces. We thus remove any dirt, scratches or grooves from the material and its surface is completely smooth after coating.
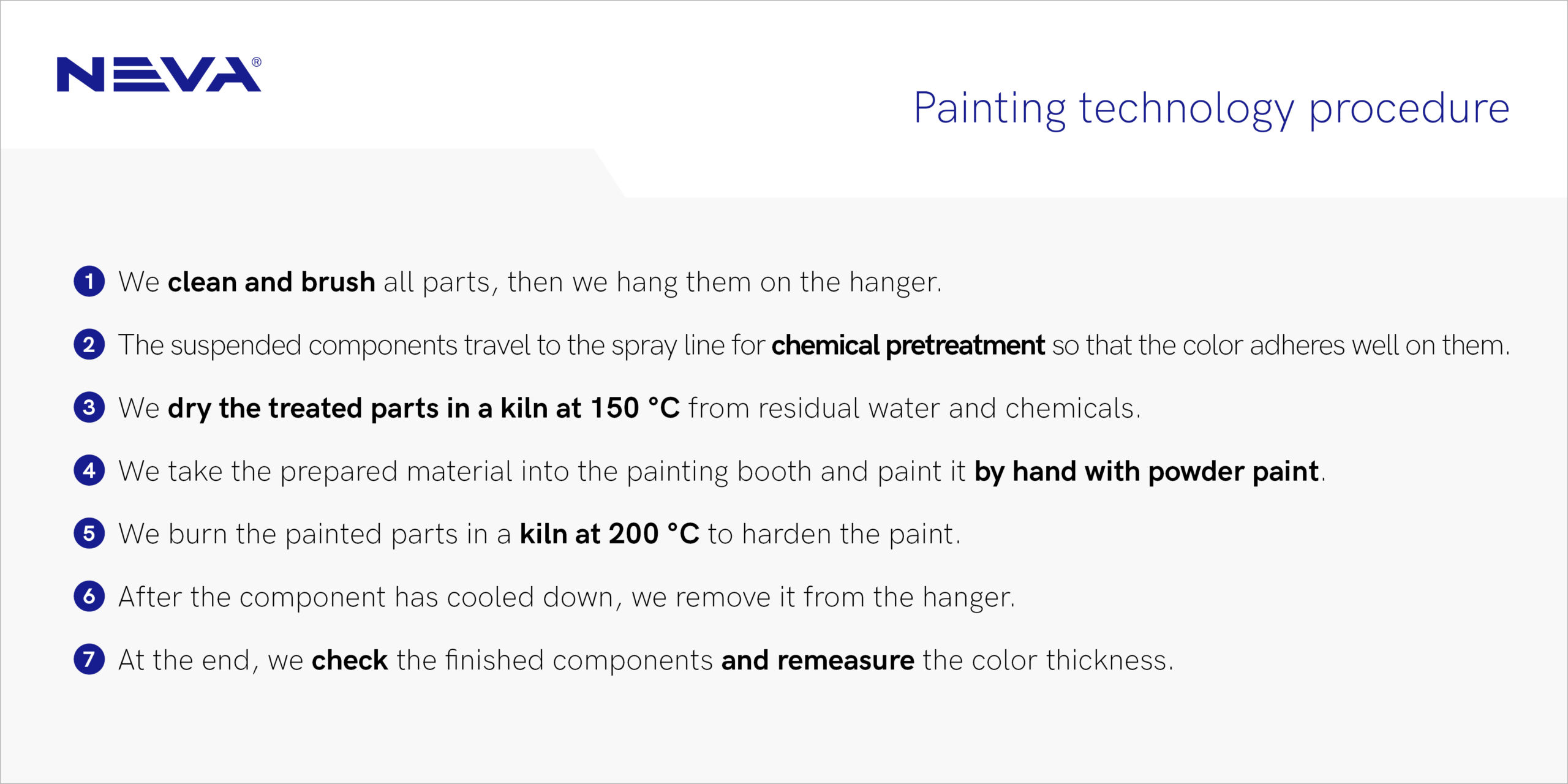
The quality of the coated components is mainly checked by women
How do things work directly in the paint booth?
We coat the blind components using a special gun. An electrostatic charge is applied to the powder coating in the gun thanks to which it adheres to the material. Two painters are always present in the booth — they stand opposite each other and each of them coats one side of the component. The coating is applied very slowly in five or six layers for the paint coat to be adequately thick and protect the material. Moreover, it must be evenly spread on the entire surface.
How do you measure the coating thickness?
The experience of the painters is important as they already know how much paint to apply to the material. After curing in the kiln and cooling, we check the thickness of the coating on the components using a digital thickness gauge. And we also focus on the visual appearance. We examine each piece — we check each corner and bend to ascertain whether too thick a paint layer has flowed in, and we check the lustre level.
Doesn’t each person judge it slightly differently?
It is certainly a subjective matter, each person has a different perception of light and colour. For this reason, we hire women for these positions. They have a better feeling for colour and appearance and are also stricter in this area. The women reject what we men would normally have released to the customer. Thanks to this, the set standard quality is very high.
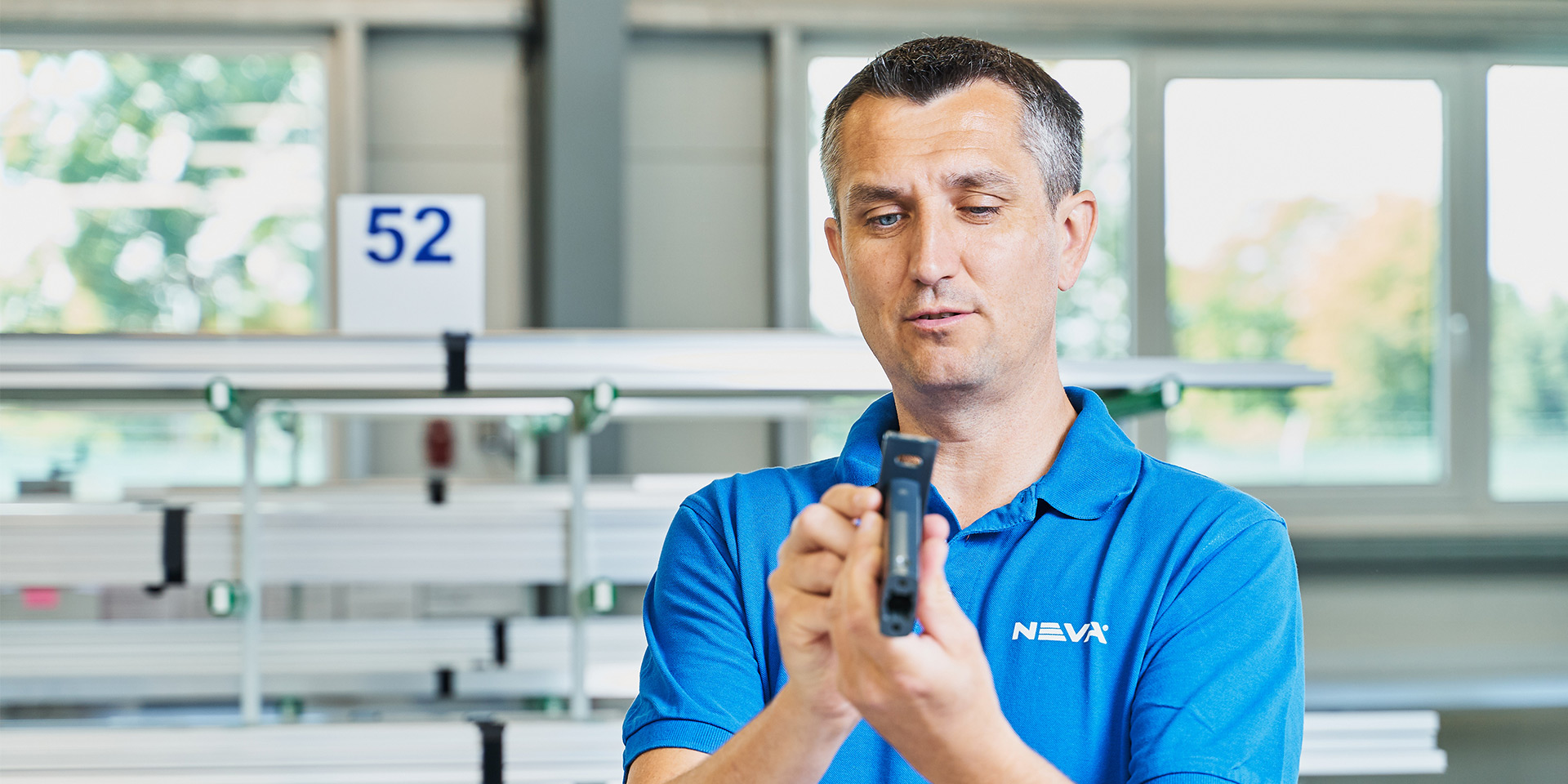
Painting is a physically and mentally demanding task
What is the most difficult task in the work of the painter?
it certainly requires patience and precision, the painter must be careful and must never hurry. When we hire a new person, it takes perhaps four or five months for him to learn and be able to do the painting himself. it is physically but also mentally demanding work.
Why?
The painters are confined to the paint booth, which is hot and noisy. They must fully concentrate while wearing overalls and full face masks, which makes talking difficult for them. And they use signals to agree on painting further material or to change paint.
Do you have any agreed signals that you use?
We do not have an actual chart of gestures, but each pair of painters already have an established gesticulation system. For instance, they wink or nod at each other.
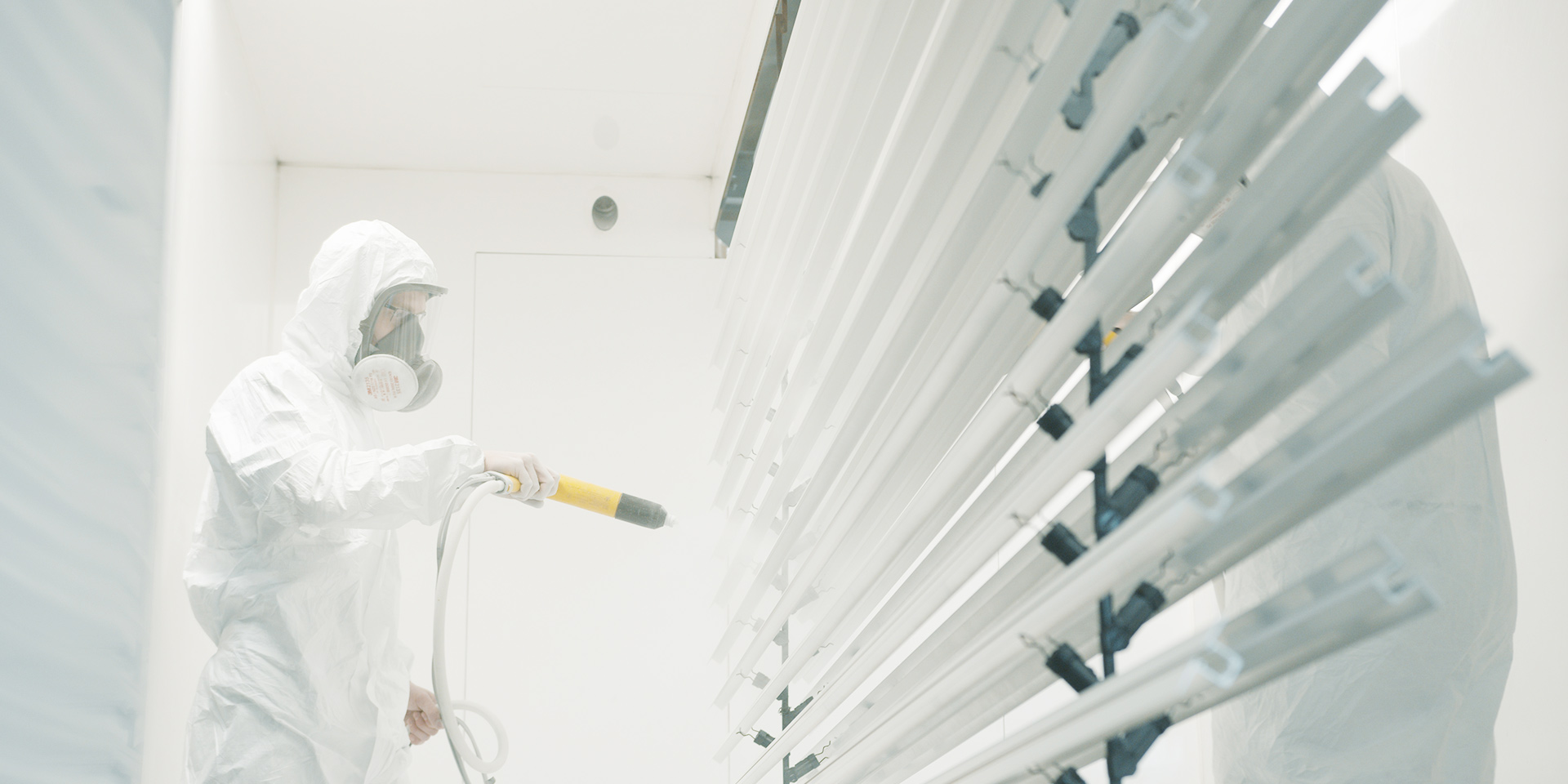
In order to prevent an explosion during the coating process, we do cleaning several times per day
Does the paint require special care?
We built a special warehouse for powder paints. For instance, the powder paint must not be exposed to direct sunlight so the warehouse is windowless. There is also a requirement for an ideal temperature and humidity, otherwise, the powder coatings would become moist and make proper application impossible. We transfer them to the paint shop a day before painting so that they can acclimatize to the paint shop conditions.
Why are cleaning and cleanliness so important?
One of the reasons is colour accuracy. If we do not clean the residual powder, the colours mix. But an even more important aspect is safety. If powder paint would collect at any point in a layer thicker than one millimetre, it just needs to be stirred up slightly and it can explode. For this reason, we must not allow powder paint deposits to collect in the paint booth and its vicinity.
One millimetre is pretty small, have you already experienced such an explosion?
Fortunately, no. We have many safety elements in the booth which prevent such a situation. Air is extracted from the entire paint booth by cyclones and filters, such that the residual powder paint is sucked out of the booth immediately. Moreover, the booth has sensors which detect ignition or air pressure, and would eventually start extinguishing the fire immediately.
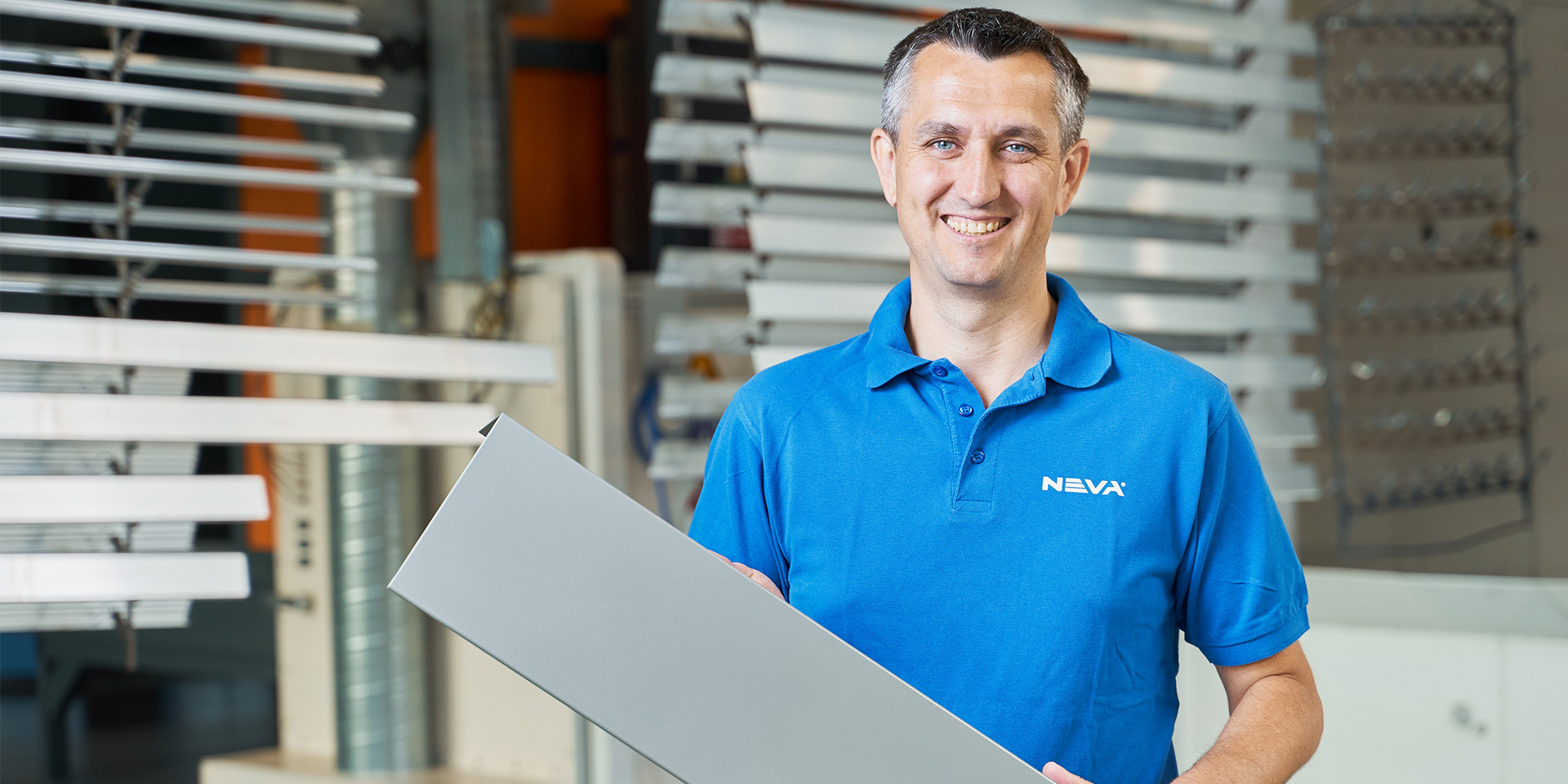
The painters change their work attire when changing to significantly different colours
How do you change the colour during the day?
We first thoroughly clean the paint that we used previously: we clean the tables and painting hoses, the entire paint booth and its exterior. Everything is blown off using compressed air, vacuum cleaned or wet cleaned. After this, we add the new colour shade to the paint gun. If we failed to do this, the paints would mix. And when changing to a significantly different colour (for instance, from black to white), the painters also change their overalls.
And how many times per day do they change work attire?
Mostly they use two overalls per shift, one for dark colour shades and one for light colour shades. For this reason it is important for us to correctly plan the powder coating sequence on a daily basis. We always make an effort to apply similar paints one after the other. We call this “grouping” — we group the orders in such a manner that the colours do not change too often. In this way, we gradually change, for instance, from black to eventually white.
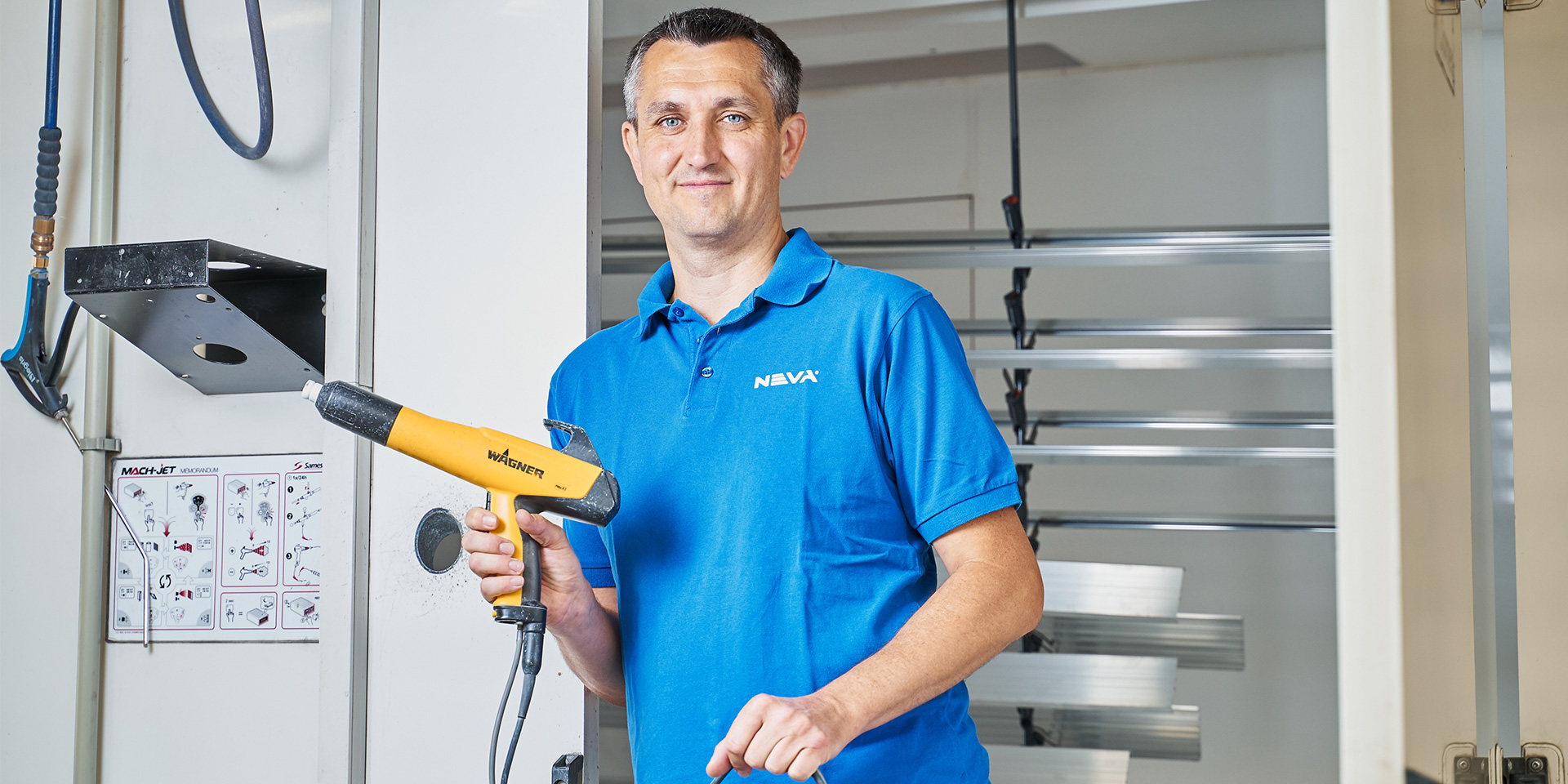
We organize tours of the powder coating plant similar to castle tours
Do customers sometimes visit the coating shop?
Our partners often visit the coating shop. We guide them through the coating shop and it seems to us that we are at a castle or chateau. They often expect the typical environment of the coating shop, which they are familiar with from wet coating — moisture and dirt. They are surprised that we do not have anything of this sort here.
How has the coating shop changed since it was established in 2014?
We focused on the working environment and installed equipment in the hall for additional extraction of hot air. That sounds rather banal, but the temperature in the hall sometimes rises to thirty-five degrees. Thanks to the air extraction, we lowered the temperature by three degrees and all the employees are thankful for this. As regards the coating process, we modified the kiln. It was initially designed for two hangers that carried the suspended components into the kiln. But the colours mixed due to air turbulence in the kiln. We thus transformed the kiln into a single hanger kiln. Moreover, this increased the speed of the line. But this is certainly not all, we are always thinking about how to make the coating shop more perfect.