NEVA under the microscope: why we are introducing lean manufacturing and what it brings to us
Lean manufacturing is aimed at higher productivity of work and more economical handling of materials. We have adopted these principles in NEVA’s department of production of ISO-KASTL (boxes), and the results have surpassed our expectations. We can now manufacture more than double the number of boxes in the same time.
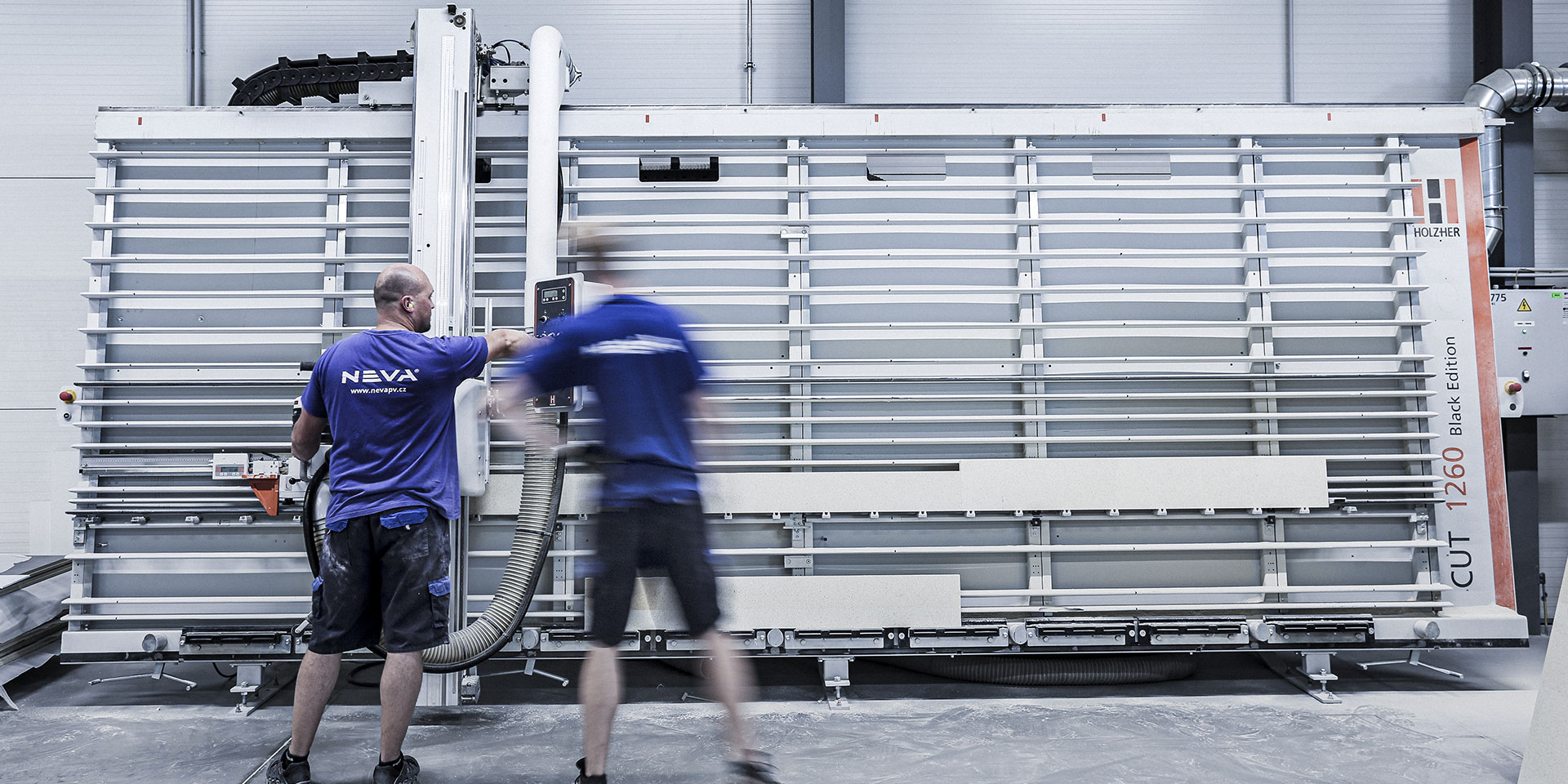
Lean manufacturing is a methodology developed by Toyota after the Second World War. It strives for the maximum optimisation of production processes to avoid any wasting of time and resources, and to ensure that the work is as efficient as possible.
Why we introduced lean manufacturing
We have been applying principles similar to lean manufacturing at NEVA for a long time. We naturally strive for as efficient production as possible and we improve it continuously, for example, by purchasing new and more advanced equipment. At the same time, we motivate our employees to help improve the production processes.
As far as equipment is concerned, we have recently bought, for example, motor-driven store racks by Proman. They will part when we need to ride between them to collect material. In this way we increased the warehouse capacity and made the work easier for the warehouse staff.
We opted to systematically introduce lean manufacturing principles last year. Of course, it was not feasible to change the running of the entire company at once. Therefore, in the first stage we set ourselves the objective of optimising the workplaces that require the greatest share of manual work. Unlike automated areas of production, it would often happen there that, for example,the employees had to wait for material, which caused downtime.
That is why we hired an external firm to help us with that.
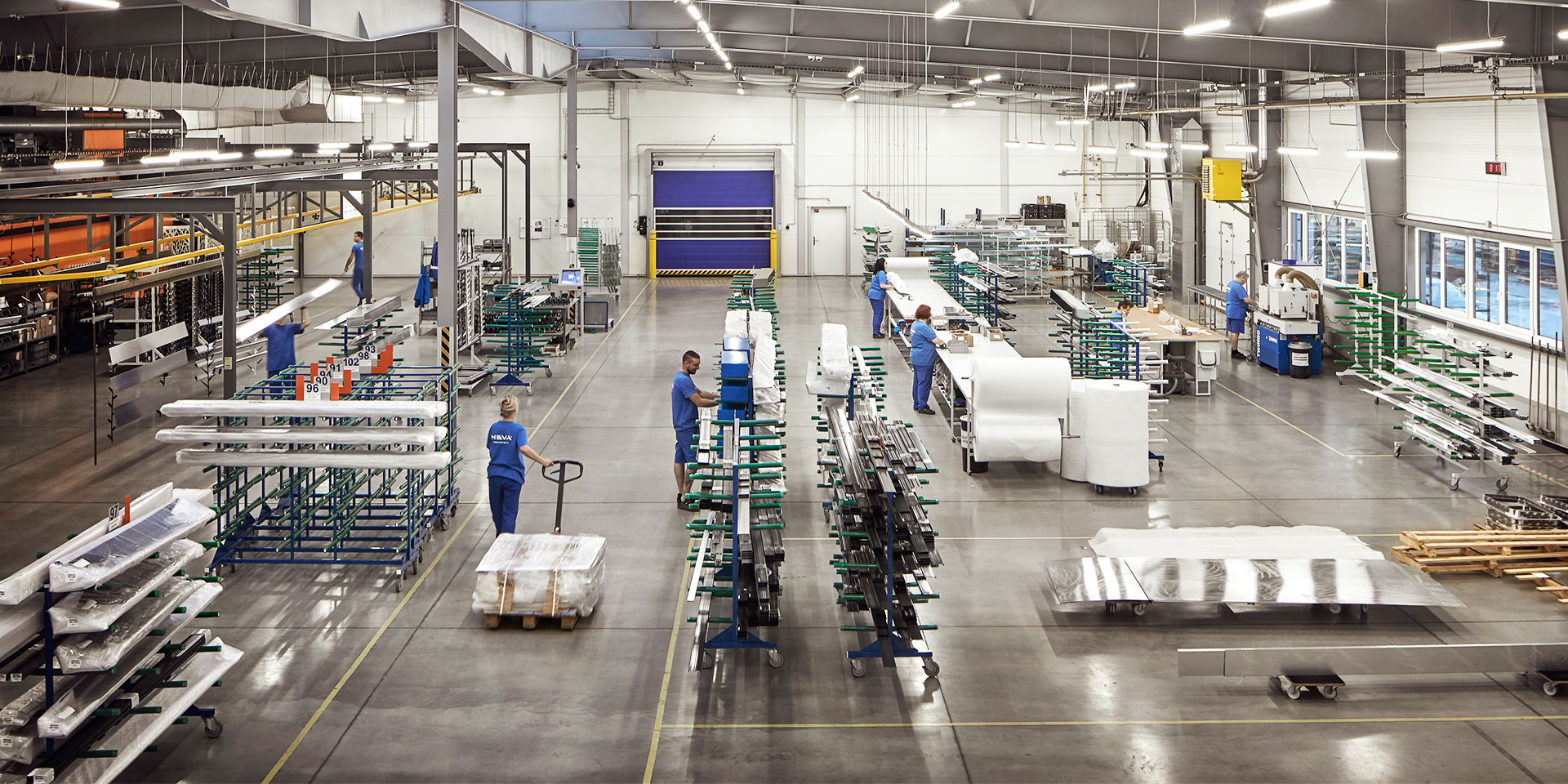
Spaghetti diagrams and optimisation of the department of ISO-KASTL boxes
The first department in which we chose to improve the processes was the production of ISO boxes, involving a significant share of manual work. Specialists from the external firm created spaghetti diagrams during the initial analysis.
In the plan of the production plant, they depicted paths along which the employees go most often and why. This resulted in proposals for how to eliminate unnecessary movement around the workplace. For example, the paints store was moved closer to the paint shop, which saved one employee up to ten minutes a day.
In addition, the ergonomics of work activities was dealt with in the blind-box plant, especially when the material is being placed. Seemingly minor improvements were often brought forward – for instance, the employees learnt that when they place the material on the right side, they will save two steps in a single operation. This totalled 20 minutes a day and several hours of saved work per one employee a month. So, even seemingly little improvements created great savings for us.
Getting the actual employees involved was of key importance as well. Even though they were initially cautious about the changes, they soon found that the main purpose of all the measures was to help them and spare them unnecessary work. In the end, the workers themselves were often coming up with suggestions for particular solutions and they were satisfied with the changes.
During evaluation we found that we had managed to save around 60% of the time and produce more than double the number of ISO boxes in the same time. That is why we decided to apply principles of lean manufacturing to other workplaces as well.