NEVA unter der Lupe: Warum wir Lean Manufacturing einführen und was es uns bringt
Das Ziel von Lean Manufacturing ist eine höhere Arbeitsproduktivität und ein sparsamerer Umgang mit Ressourcen. Diese Prinzipien setzten wir bei NEVA in der Produktionsabteilung von ISO-KASTEN um und die Ergebnisse übertrafen unsere Erwartungen. Im Vergleichszeitraum werden wir mehr als die doppelte Anzahl an Kasten produzieren.
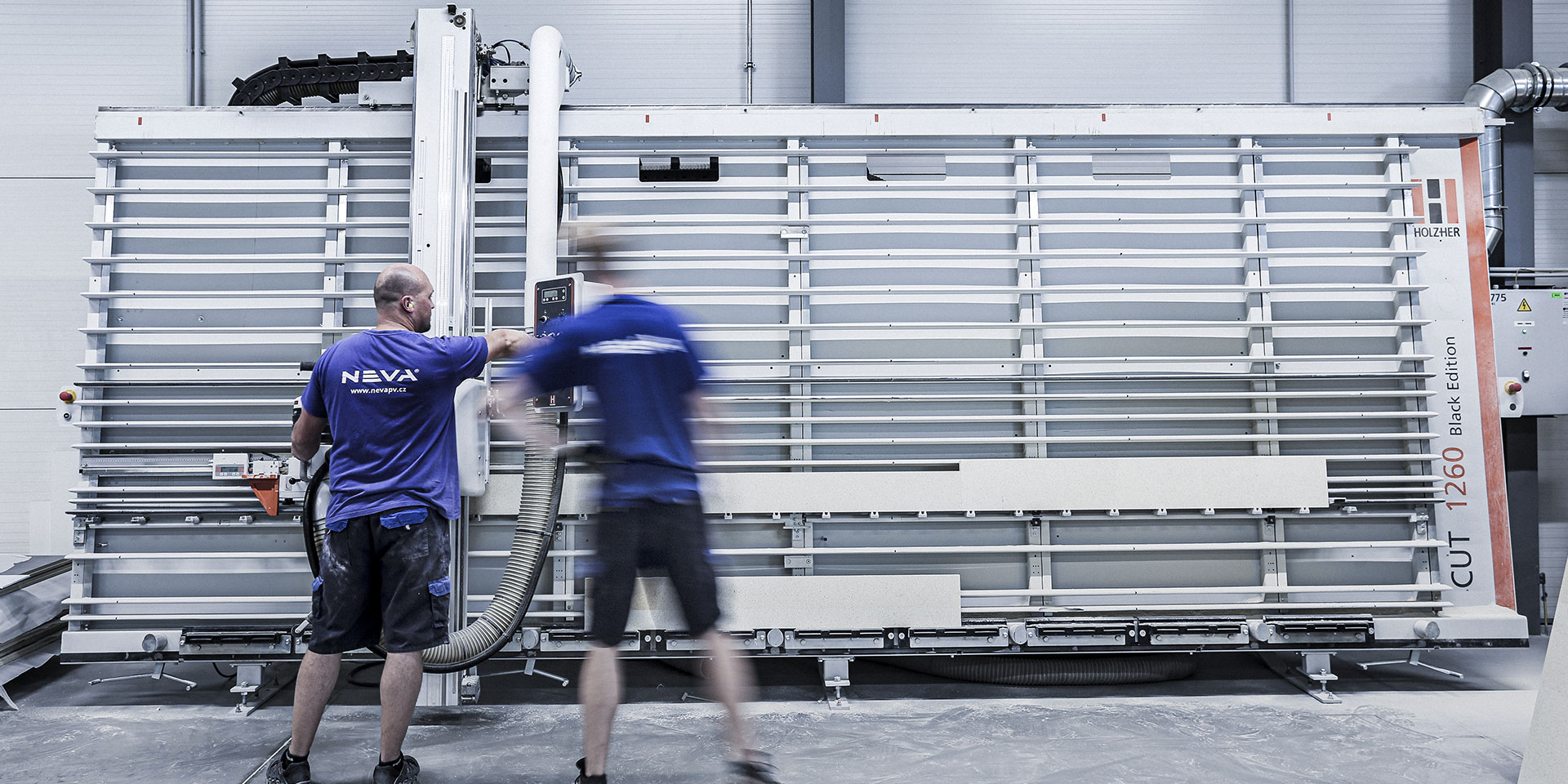
Lean Manufacturing ist eine Methode, die Toyota nach dem Zweiten Weltkrieg entwickelte. Diese zielt darauf ab, die Optimierung von Produktionsprozessen zu maximieren, um Zeit‑, Ressourcen- und Arbeitsverschwendung zu vermeiden, damit die Arbeitsprozesse so effizient wie möglich ablaufen.
Warum wir Lean Manufacturing einführten
Wir verwenden bei NEVA seit langem Prinzipien, die an Lean Production angelehnt sind. Selbstverständlich streben wir nach der effizientesten Produktion und verbessern diese kontinuierlich, zum Beispiel durch die Anschaffung neuer und modernerer Anlagen. Gleichzeitig motivieren wir unsere Mitarbeiter, damit sie die Produktionsprozesse verbessern helfen.
Bei der Ausstattung kauften wir zum Beispiel Lagerregale der Marke Proman, die elektrisch angetrieben werden und mobil sind. Sie „treten“ auseinander, wenn wir zwischen ihnen hindurchfahren und Material entnehmen. Damit erhöhten wir die Kapazität des Lagers und erleichterten den Lagermitarbeitern die Arbeit.
Wir entschieden uns im vergangenen Jahr, die Prinzipien des Lean Manufacturing konsequent umzusetzen. Natürlich war es unrealistisch, die Funktionsweise des gesamten Unternehmens auf einmal zu ändern. In der ersten Phase setzten wir uns daher zum Ziel, diejenige Arbeitsplätze zu optimieren, die den größten Anteil an Handarbeit erfordern. Im Gegensatz zu den automatisierten Teilen der Produktion kam es mitunter vor, dass Mitarbeiter beispielsweise auf Material warten mussten, was zu Ausfallzeiten führte.
Deshalb beauftragten wir eine externe Firma, uns dabei zu helfen.
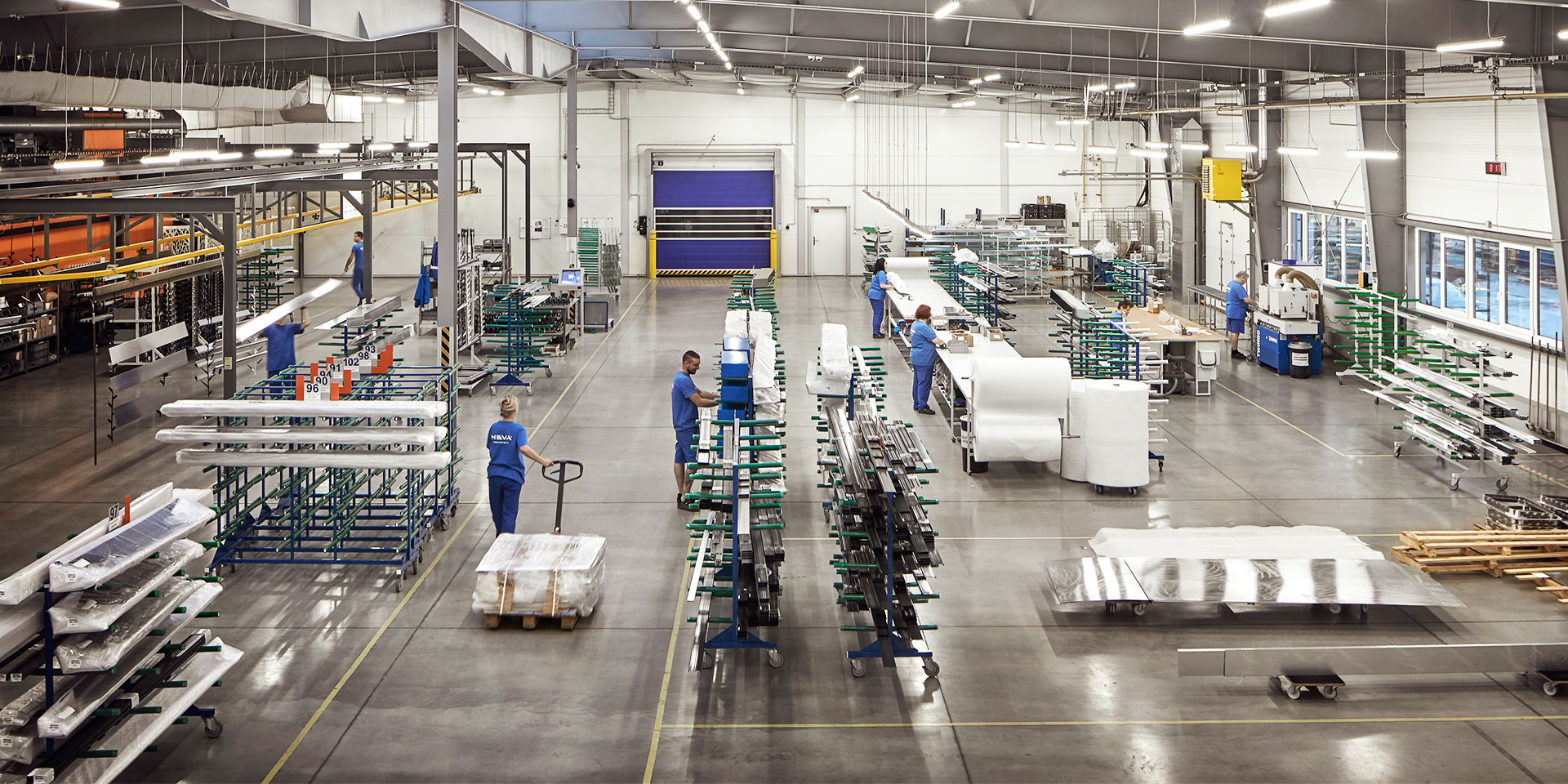
Spaghetti-Diagramme und Optimierung der Abteilung ISO-KÄSTEN
Zunächst entschieden wir uns für die Verbesserung der Produktionsabteilung für ISO-KÄSTEN, in der ein erheblicher Anteil an Handarbeit anfällt. Bei der ersten Analyse erstellten die externen Fachleute sogenannte Spaghetti-Diagramme.
Auf dem Situationsplan der Produktionsstätte zeigten sie die Wege, welche und aus welchen Gründen die Mitarbeiter am häufigsten gehen. Daraus entstanden Vorschläge, wie unnötige Bewegung am Arbeitsplatz vermieden werden kann. So ist beispielsweise das Lacklager näher an die Lackiererei gerückt, was einem Mitarbeiter bis zu zehn Minuten pro Tag einspart.
Weiter wurde die Ergonomie der Arbeitstätigkeiten bei der Herstellung von Rollladenkästen, insbesondere beim Verlegen des Materials, verbessert. Oft wurden scheinbar kleine Verbesserungen vorgenommen – die Mitarbeiter lernten zum Beispiel, dass durch das Auflegen des Materials auf die rechte Seite zwei Arbeitsschritte pro Arbeitsgang eingespart werden. Dies machte insgesamt 20 Minuten Zeiteinsparung pro Tag aus, was pro Mitarbeiter und Monat insgesamt eine Zeiteinsparung von mehreren Stunden bedeutet. Selbst die scheinbar kleinen Verbesserungen waren für uns eine große Einsparung.
Wichtig war auch, die Mitarbeiter selbst einzubeziehen. Obwohl sie anfangs den Veränderungen gegenüber skeptisch waren, stellten sie bald fest, dass alle Maßnahmen hauptsächlich dazu dienten, ihnen zu helfen und unnötige Arbeit zu eliminieren. Am Ende machten die Mitarbeiter oft selbst Vorschläge für konkrete Lösungen und waren mit den Veränderungen zufrieden.
Bei der Auswertung stellten wir fest, dass es uns gelungen ist, rund 60 % der Zeit einzusparen und im gleichen Zeitraum mehr als die doppelte Anzahl an ISO-KÄSTEN zu produzieren. Daher entschieden wir uns, die Prinzipien des Lean Manufacturing auch auf weitere Arbeitsplätze auszuweiten.