NEVA sous la loupe : pourquoi nous mettons en place le lean manufactoring et ce que cela nous apporte
L’objectif du lean manufactoring est d’augmenter la productivité du travail et de faire des économies de matières premières. Ces deux principes ont été mis en place chez NEVA, dans le service de fabrication des ISO-KASTL, et les résultats obtenus ont dépassé nos attentes. À temps identique, nous fabriquons désormais deux fois plus de coffres.
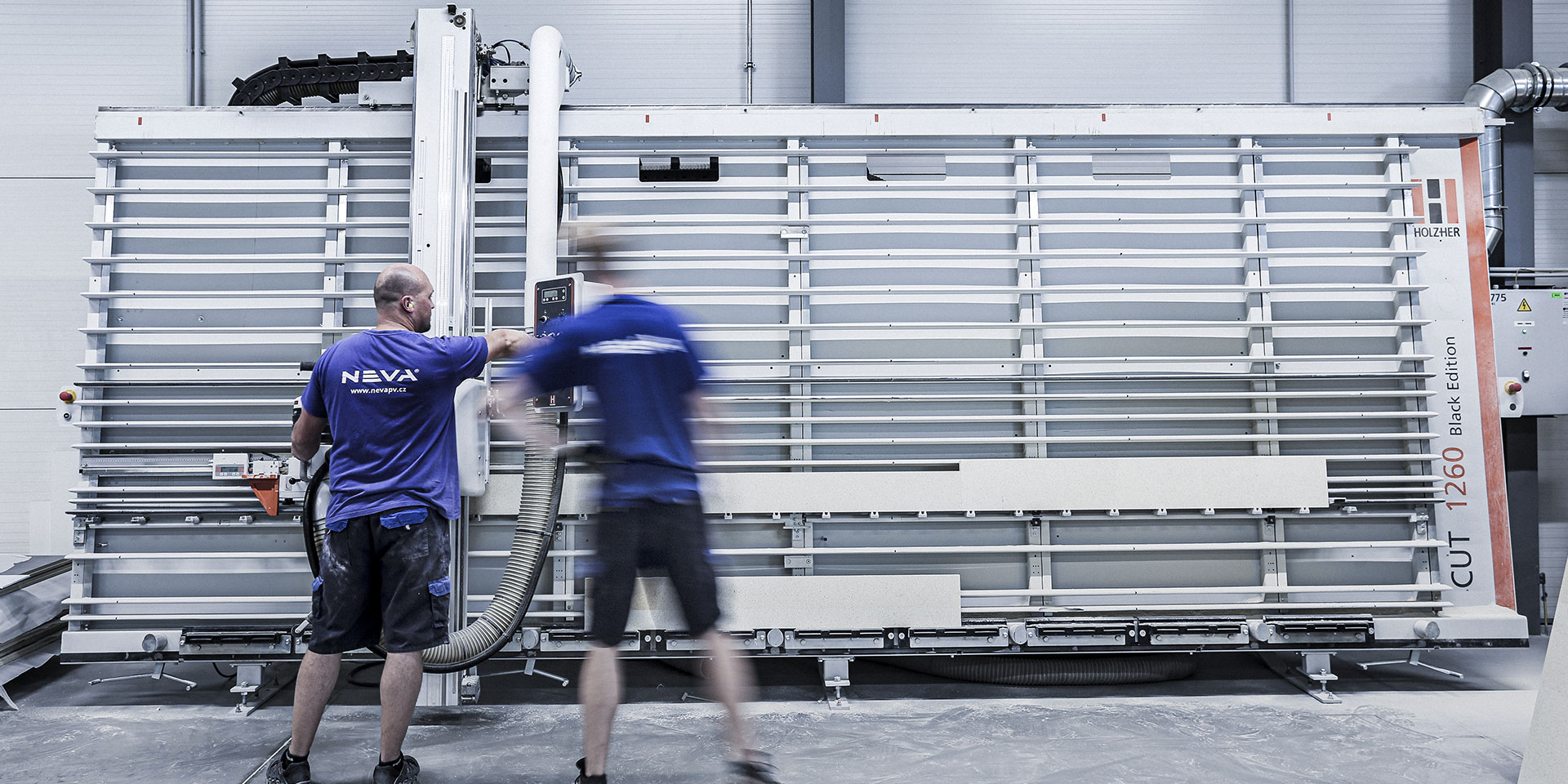
Le lean manufacturing est une méthode qui a été développée par la société Toyota après la seconde guerre mondiale. L’objectif est une optimisation maximale des processus de fabrication pour éviter les pertes inutiles de temps et de matières premières, et pour rendre le travail plus efficace dans son ensemble.
Pourquoi avons-nous mis en place le lean manufactoring
NEVA utilise des principes semblables à ceux du lean manufacturing depuis longtemps. Nous avons toujours fait le maximum pour améliorer l’efficacité de notre production et nous y apportons donc continuellement des améliorations en achetant par exemple des nouveaux équipements plus modernes. Nous motivons également nos employés pour qu’ils contribuent aussi à l’amélioration des processus de production.
En ce qui concerne les équipements, nous avons dernièrement acheté des rayonnages d’entrepôt motorisés de la société Proman. Ceux-là se déplacent aisément lorsque vous avez besoin de passer entre eux pour aller déstocker certaines matières premières. Nous avons ainsi augmenter la capacité de l’entrepôt tout en simplifiant le travail de nos magasiniers.
Mais l’année dernière, nous avons réellement décidé de systématiquement mettre en place un système de lean manufactoring. Il était évidemment hors de question de totalement modifier notre fonctionnement du jour au lendemain. Nous nous sommes donc donnés comme premier objectif d’optimiser les postes qui exigent le plus de travail manuel. À la différence des postes qui sont automatisés, il arrivait souvent que nos collaborateurs doivent y attendre l’arrivée des matières premières, ce qui entraînait des temps morts dans leur travail.
Nous avons donc demandé à une entreprise externe de nous aider à mettre en place des améliorations.
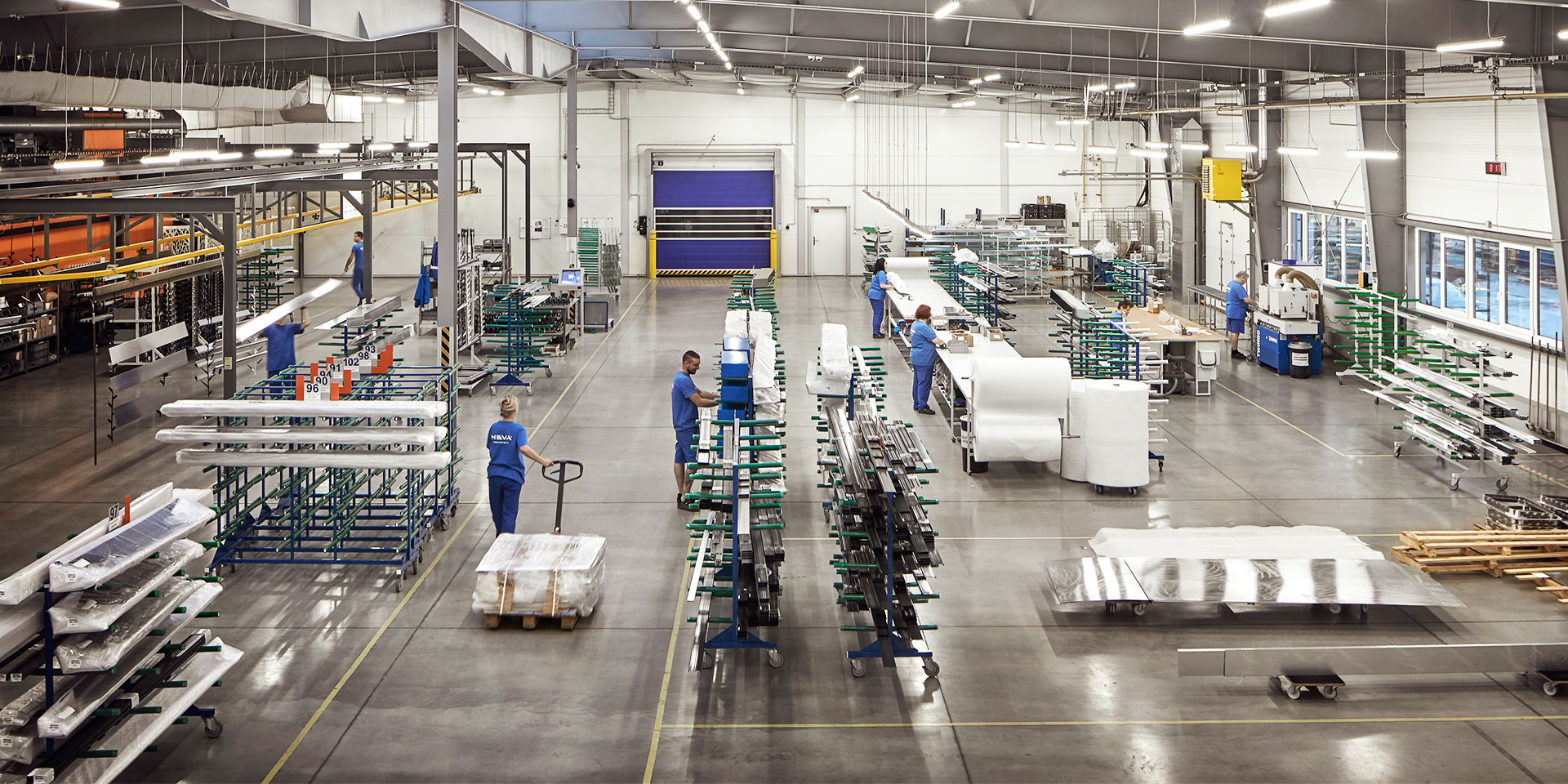
Les diagrammes spaghetti et l’optimisation du service des coffres ISO-KASTL
Nous avons décidé de commencer à améliorer les processus de production dans le service de fabrication des coffres ISO-KASTL car ils exigent une grande part de travail manuel. Les premières analyses des spécialistes de l’entreprise externe chargée de l’optimisation ont permis de créer des diagrammes dits spaghettis.
Sur un plan des espaces de production, ils ont illustré les zones de passages les plus fréquents et les raisons pour lesquelles les employés les suivent. Cela leur a permis de faire des propositions pour éliminer les mouvements inutiles sur le poste de travail. Le stock de peintures a par exemple été déplacé plus près de l’atelier de peinture, ce qui a permis à notre personnel de gagner dix minutes par jour.
Le second point étudié sur le poste de fabrication des coffres de stores concernait l’ergonomie des activités de travail, notamment lors de la pose des matériaux. Ce sont souvent de petites améliorations qui ont été permises : le personnel a par exemple appris qu’en posant les matériaux à droite, il peut économiser deux pas par opération, ce qui constitue un total de 20 minutes par jour et donc de plusieurs heures d’économie de travail par employé et par mois. De toutes petites améliorations peuvent donc aussi constituer de grands gains de temps.
Il a également été essentiel d’impliquer nos employés dans la mise en place de ces nouvelles procédures. Bien qu’un peu réticents au départ, ils ont vite compris que ces mesures avaient pour principal objectif de les aider et de leur économiser du travail inutile. Au final ce sont nos employés eux-mêmes qui proposaient des solutions concrètes et ils se sont même avérés être très contents des modifications apportées.
Lors de l’évaluation de ce processus, nous avons pu constater que nous étions parvenus à économiser environ 60 % du temps tout en produisant plus du double de coffres ISO KASTL pendant la même période. Nous avons donc décidé d’appliquer les principes de lean manufactoring aux autres postes de travail.