What does it look like in our warehouse?
In order to grow and ensure smooth operations, the warehouse needs to run perfectly. That is why we pay great attention to its organisation. In the past, we shared news of lean manufacturing implementations that save the warehouse personnel time. But this is not the only improvement. What does the NEVA warehouse look like today?
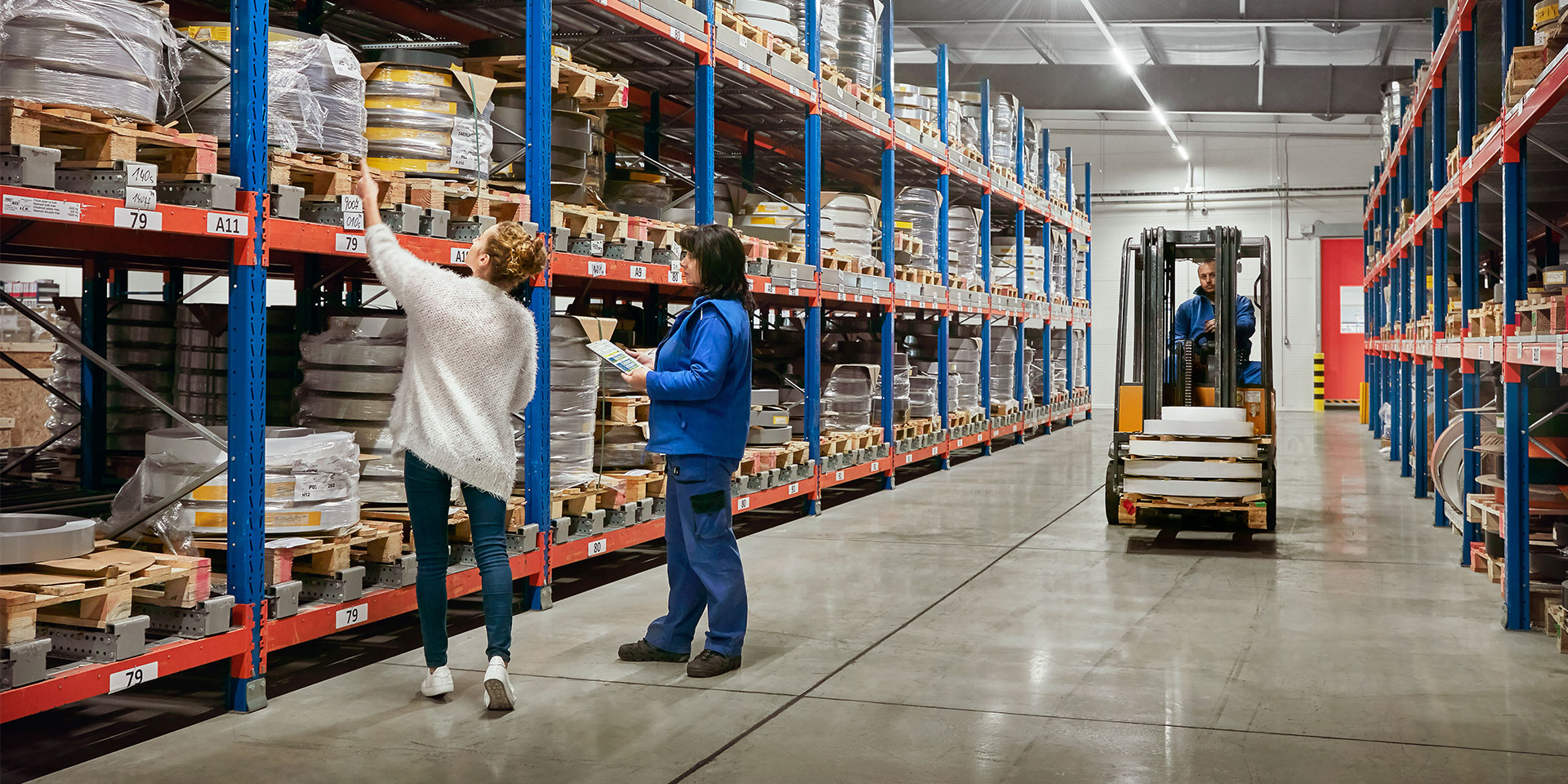
In our warehouse, we receive daily deliveries of lamella scrolls, profiles, sheets, motors or packaging material to ensure the production of our products. We also ship finished external blinds or screen roller shutters to our partners in the Czech Republic and abroad. So there is always something going on in the warehouse. That is why we consistently maintain proper order and safety.
The Helios information system helps us keep track of data for successful company management. We use readers for systematic material flows. This way, we have an overview of all material flows. We are currently working on a new system that will make the process and company management even more efficient.
Lean manufacturing — what does it entail?
Our goal is to continuously improve processes, the work environment, increase efficiency and reduce waste. We therefore purchase materials on the basis of a minimum quantity set in order to meet customer demand. This saves space in the warehouse where nothing hangs around for long.
As our Head of Internal Logistics, Dávid Kasaj, says: “In order to meet the customer demand and smooth material flows, we need to set up processes thoroughly and continuously improve them.”
Warehouse staffing is based on lean manufacturing practices. We place goods in the warehouse in the most suitable place so that they are easy to access — material with faster turnover is placed at the front, material with slow turnover at the back. The same applies to warehouse keepers’ accessories. Everything has its place. We keep the workplace clean so that everyone feels comfortable and enjoys working here.
Based on efficiently set processes and organisation, the warehouse can ensure that production always has the right material at the right time, in the right place and in the right quantity. With clearly defined processes, we can produce from 2,300 to 2,500 external blinds per week.
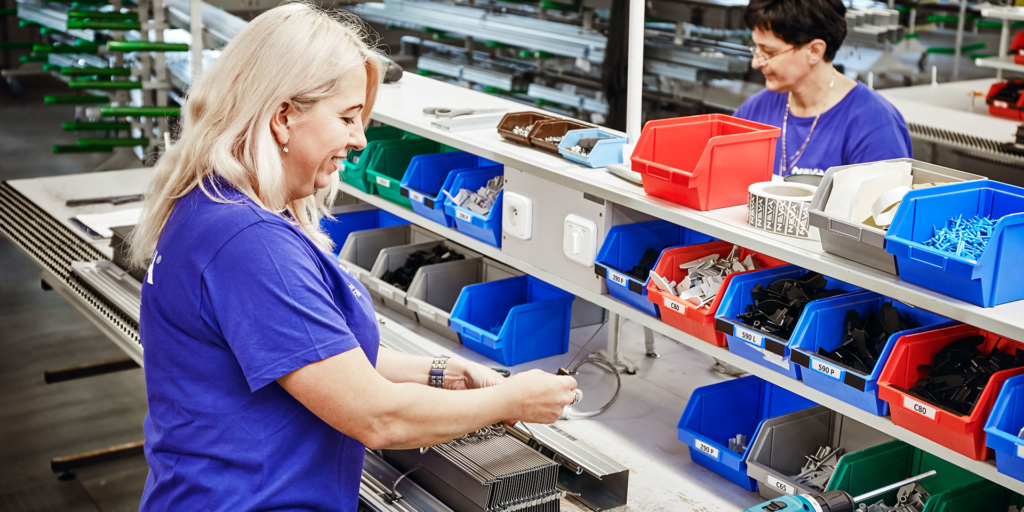
We follow lean production principles in the organisation of our work
We use a number of lean manufacturing methodologies, such as Kanban, 5S, Daily Kaizen, Standardization, TPM, Smed, Visual Management and others.
The above-mentioned 5S method for work organisation originated in Japan. It refers to a set of five guidelines for clear and efficient production:
- Seiri — means sort. We leave only the really necessary tools in the workplace. We put back the unnecessary ones in their place.
- Seiton — straighten. It refers to the need for systematization and a schedule of work where each task is broken down step by step.
- Seiso — shine. We keep the workplace clean.
- Seiketsu — standardize the above 3 Ss. Each worker should experience the entire process with clearly defined tools.
Shitsuke — sustain to improve and maintain. The whole process of the previous 4 Ss should be followed, which requires discipline. But at the same time, it should be continually tested, improved and streamlined.
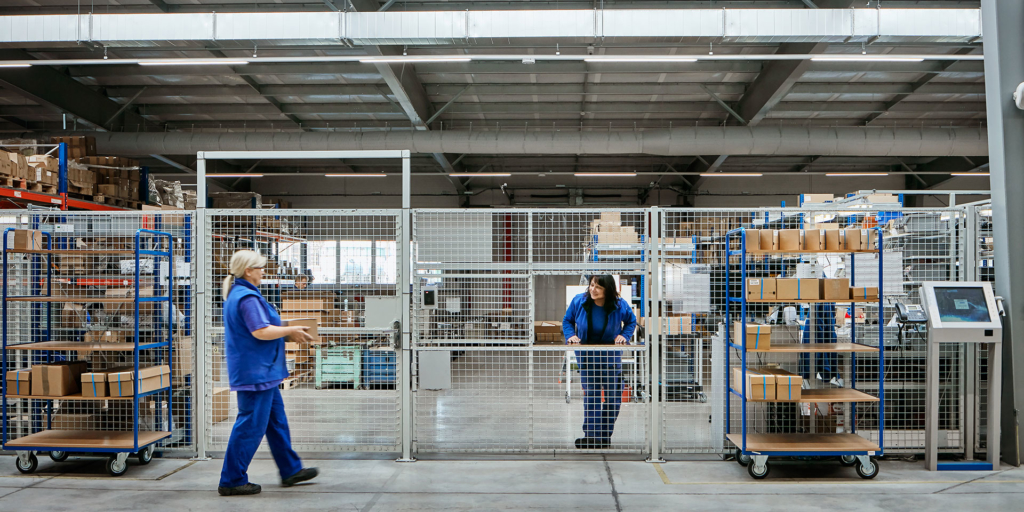
Automation is not detrimental to the personal approach
As you can see from the points above — to be more efficient, we are constantly improving our work. Dávid Kasaj confirms this: “We are constantly trying to improve our processes, adapting to modern trends in storage and process setting. In this respect, we are really open to new ideas.”
To ensure maximum utilisation of storage capacity, we use mobile cantilever racks and vertical storage towers.
Similar streamlining will come with the new cutting centre, which will cut profiles faster and more accurately. In addition, we will ensure fewer errors and less waste.
But people are still irreplaceable and at NEVA we understand the value of a satisfied team. The good conditions we have in the workplace are also visible externally. As Ladislav Just from MetalPlast said, “I was very satisfied with the environment in which the people at NEVA work. There is nothing rolling around on the floor and the overall layout of the issue station was also clear.”
Similarly, Jiří Rosecký from Diamond Design praises NEVA’s internal organisation: “The organisation of production is a sign of how the supplier works. I was fascinated by the sophisticated system, good order and cleanliness in NEVA production. I am not exaggerating when I say that you could eat off the floor there. And that is quite unique in this industry.”